Keg Pressure: Essential Tips for Optimal Beer Quality
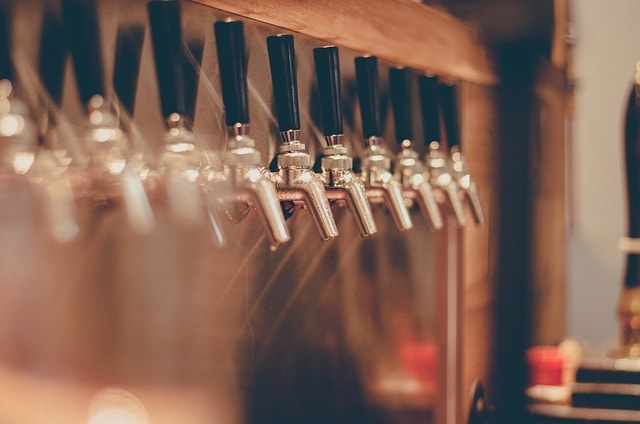
For anyone who enjoys draft beer, understanding keg pressure is crucial for achieving the perfect pour. Proper keg pressure ensures that the beer maintains its flavor and carbonation from the keg to the glass. Avoiding low pressure is essential to prevent flat beer. The ideal serving pressure generally ranges between 12-14 PSI, but it may vary depending on the type of beer, temperature and gas blend.
Keg pressure plays a vital role in the dispensing process. It balances the carbonation levels and influences the taste of the beer. Setting up your keg system correctly, including adjusting the pressure, ensures a smooth and enjoyable experience. Beer enthusiasts need to pay attention to factors like line length and resistance to maintain the right pressure.
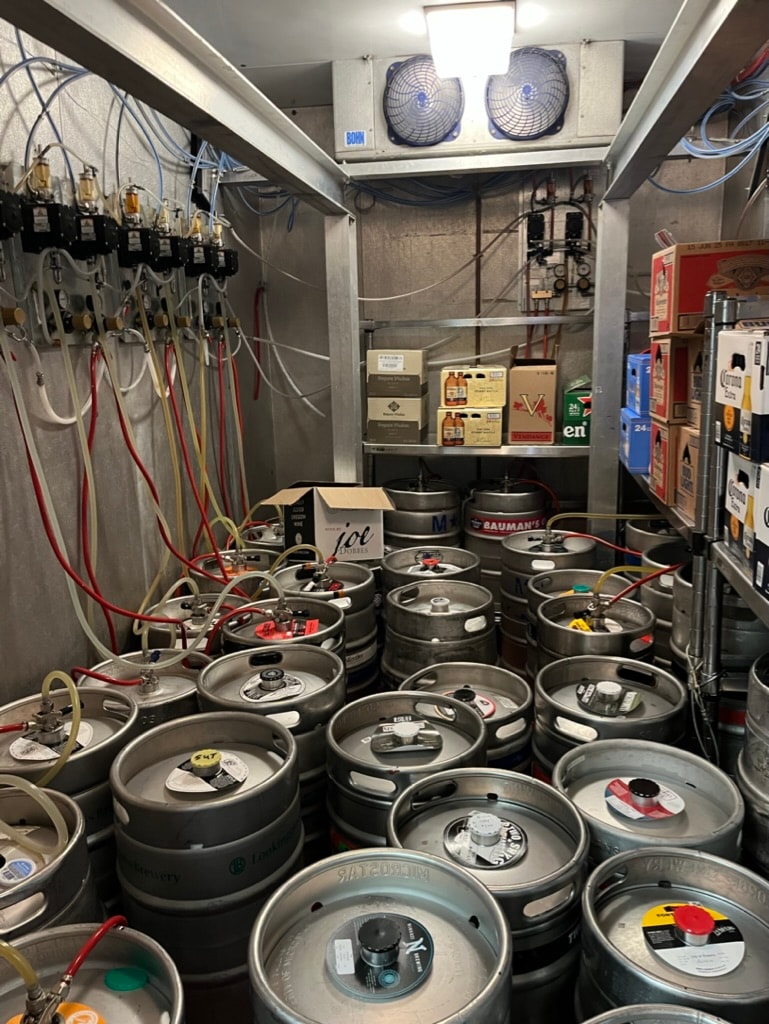
Temperature control is another important aspect when handling keg pressure, as temperature changes can affect carbonation. Keeping the beer at the right temperature helps in maintaining both pressure and taste. By understanding these elements, beer lovers can enjoy the best flavors from their draft systems.
Key Takeaways
- Ideal keg pressure is usually 12-14 PSI.
- Proper setup and maintenance are key to good keg pressure.
- Temperature control affects carbonation and pressure.
Basics of Keg Pressure
Keg pressure plays a vital role in maintaining beer quality and taste. Understanding how pressure levels, measured in psi, affect carbonation and the role of CO2 can help ensure the perfect pour. Cask ale is another form of beer that requires different handling compared to keg beer.
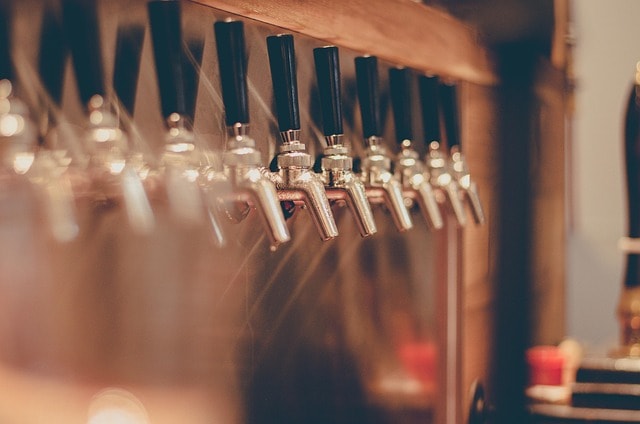
Understanding PSI
PSI, or pounds per square inch, is the unit used to measure pressure within a keg. It's crucial for maintaining the right carbonation level in the beer. Typically, ale and lager beers require a pressure setting between 12 and 14 psi. This range helps preserve the carbonation that creates the beverage’s crisp and refreshing feel.
Adjusting psi is necessary based on the type of beer and environment. If the pressure is too low, beer can become flat and lack carbonation. On the flip side, high pressure can lead to excessive foam and alter the taste. By carefully setting psi, brewers can maintain consistent quality, ensuring the beer tastes as intended.
Role of CO2 in Carbonation
CO2 is critical for keeping beer carbonated and enhancing its flavor. It is dissolved in the beer under pressure, typically measured in volumes of CO2. This refers to the amount of CO2 gas dissolved in liquid, impacting the fizz and mouthfeel of the beer.
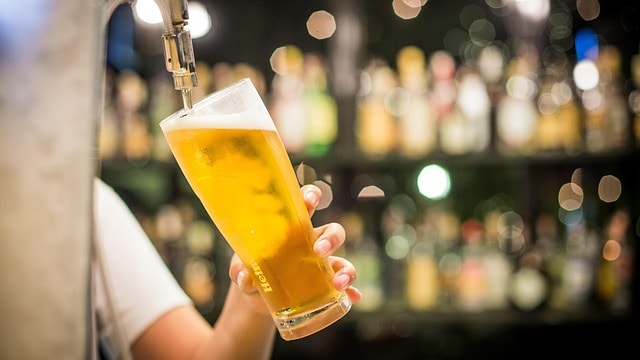
Different styles of beer require varying CO2 levels for ideal carbonation. For instance, lighter beers may require higher volumes of CO2 compared to heavier, maltier beers. CO2 not only aids in carbonation but also acts as a preservative by preventing the oxidation of beer. Properly managing CO2 levels ensures balanced carbonation and freshness from keg to glass.
Understanding Draft Beer Systems
What is a Draft Beer System?
A draft beer system is a network of components that work together to dispense beer from a keg to a faucet. The system typically consists of a keg, a regulator, a gas line, a beer line, and a faucet. The keg stores the beer under pressure, while the regulator controls the pressure of the gas line, which delivers the beer to the faucet. The beer line carries the beer from the keg to the faucet, and the faucet dispenses the beer to the consumer.
A well-designed draft beer system is essential for serving high-quality draft beer. It ensures that the beer is dispensed at the correct temperature, pressure, and flow rate, which affects the flavor, aroma, and overall drinking experience.
Whether in a bustling bar, a cozy restaurant, or a homebrewing setup, a properly maintained draft beer system guarantees that every pour is perfect.
Setting Up Your Draft Beer System
Setting up your keg correctly ensures the right pressure and carbonation, leading to the best beer quality. A draft system plays a crucial role in maintaining proper pressure settings by efficiently delivering keg beer from a temperature-controlled environment. It’s crucial to get the details right and focus on vital components like pressure relief valves.
Using a Pressure Relief Valve
A pressure relief valve is an essential component in maintaining proper keg pressure. This valve allows the release of excess gas to prevent over-pressurization, which can lead to foamy or flat beer. During the setup, ensure the valve is functioning properly by gently pulling on the ring at the top. This action should release any excess pressure, allowing the beer to carbonate correctly.
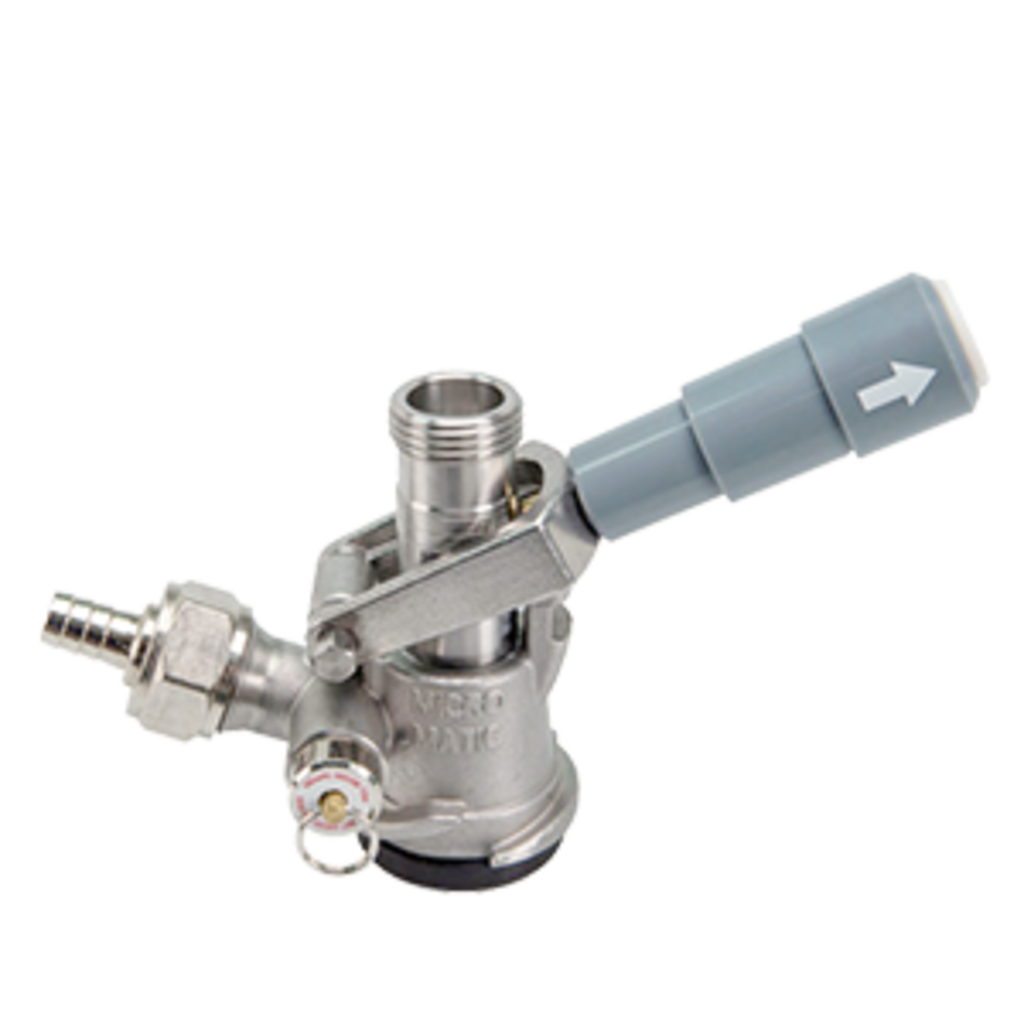
Carefully adjusting the pressure settings is important. If the pressure is too high, the beer will be overly carbonated, and if too low, it will be flat. Monitor the keg pressure regularly, using the valve to make any necessary adjustments. Utilizing a pressure relief valve ring ensures optimal beer quality and drinking enjoyment.
Additionally, the sample valve on kegs can help in checking beer clarity and carbonation levels without releasing too much pressure. Ensuring all valves and connections are secure and free of leaks is paramount in keeping the system running smoothly.
Determining the Right Pressure
Factors Affecting Keg Pressure
Keg pressure is a critical factor in a draft beer system, as it affects the flow rate and quality of the beer. Several factors can influence keg pressure, including:
- Carbonation Pressure: This is the pressure required to maintain the desired level of carbonation in the beer, typically measured in volumes of CO2. Different beer styles require different carbonation pressures to achieve their characteristic fizz and mouthfeel.
- Serving Pressure: The pressure at which the beer is dispensed from the faucet, usually measured in pounds per square inch (PSI). Serving pressure needs to be carefully adjusted to ensure the beer flows smoothly without excessive foaming or flatness.
- Line Length and Resistance: The length and resistance of the beer line can significantly impact the pressure needed to dispense the beer. Longer lines and higher resistance require higher pressure to maintain the desired flow rate. Using a line length calculator can help determine the optimal pressure settings.
- Elevation: The elevation of the keg and faucet can also affect the pressure required to dispense the beer. Kegs located at higher elevations need higher pressure to compensate for the increased pressure drop due to gravity.
- Temperature: The temperature of the beer and the environment can influence the pressure required to dispense the beer. Warmer temperatures generally require higher pressure to maintain the desired flow rate and carbonation levels.
By understanding and balancing these factors, you can ensure that your draft beer system delivers the perfect pour every time.
Line Length and Resistance
Beer Line Length and Elevation
Beer line length and elevation are critical factors in determining the pressure required to dispense beer from a keg. The length of the beer line affects the pressure drop, which can result in a lower serving pressure at the faucet. The elevation of the keg and faucet also impacts the pressure needed, as gravity can either assist or hinder the flow of beer.
To determine the ideal beer line length and elevation, brewers can use a line length calculator or consult with a draft beer system expert. The calculator takes into account the keg pressure, serving pressure, line length, and elevation to determine the optimal line length and pressure required to dispense the beer.
In general, it is recommended to keep the beer line as short as possible to minimize pressure drop and ensure a consistent serving pressure. However, this may not always be feasible, especially in commercial settings where the keg and faucet are located at different elevations. In such cases, brewers can use a combination of line length and elevation adjustments to determine the ideal pressure required to dispense the beer.
By carefully considering beer line length and elevation, you can optimize your draft beer system to deliver a perfect pour, ensuring the beer flows smoothly and maintains its intended flavor and carbonation.
Maintaining Proper Keg Pressure
Proper keg pressure is crucial to ensure a smooth and enjoyable beer-pouring experience. Calculating beer lines and line lengths is essential to maintain proper pressure and avoid foaming. Key factors include monitoring the PSI levels and troubleshooting any fluctuations in pressure to maintain the right carbonation level.
Regular Monitoring
Regularly checking the keg's PSI setting is essential to maintain proper carbonation and pouring quality. The recommended pressure usually falls between 12-14 PSI CO2 for standard ales and lagers. For other beer types, the ideal pressure might vary slightly based on the desired carbonation level, and length of run.
It’s important to have a reliable pressure gauge to check these levels frequently. Adjustments can easily be made using the beer regulator to achieve the desired settings. Storage conditions also play a role; make sure that the kegs are stored at a constant temperature to prevent any pressure variations. Ensure that the CO2 tank is appropriately filled, as low levels can lead to inconsistent pressure delivery.
Proper sealing of the keg system is another factor that can affect pressure. A leak in the connection can disrupt the PSI setting and cause CO2 loss. Regular checks on the seals and connections can prevent such issues from arising.
Troubleshooting Fluctuations
When pressure varies unexpectedly in a keg system, it can lead to undesirable beer quality, such as excessive foaming or flatness. It is important to identify and troubleshoot low pressure issues to ensure optimal carbonation levels and beer quality. The first step to troubleshoot this is to examine the CO2 tank gauge. Ensure that the CO2 level is adequate and there is no leakage.
Next, review the beer regulator settings. If adjustments have been made recently, ensure they reflect your specific beer’s requirements. Check that all connections are secure and free from leaks by using a soapy water solution to identify escaping gas bubbles.
Another common issue is temperature fluctuations. If the keg is stored at varying temperatures, this can affect carbonation and pressure. Keep the storage environment consistent and insulated if possible.
In addition, keep an eye out for blockages in the beer line that can cause pressure build-up and disrupt flow. Regular cleaning can help prevent these issues and maintain smooth operation.
Importance of Temperature Control
Controlling the temperature is key to ensuring the best quality pour from a keg system. This is crucial for maintaining the desired beer flavor and optimizing settings in a kegerator.
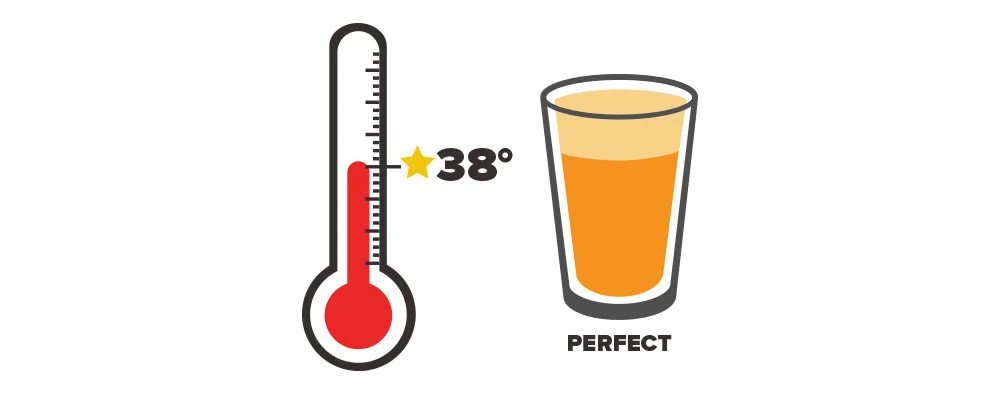
Impact on Beer Quality
Beer temperature plays a vital role in the quality of the pour. If beer is too warm, it tends to foam excessively, resulting in a less pleasant drinking experience. On the other hand, beer that's too cold may suppress the flavors and aromas, reducing overall enjoyment.
A well-maintained temperature range ensures consistency in taste and carbonation levels. The ideal temperature for dispensing lager is typically between 36-38°F, whereas ales might be slightly warmer at around 38-42°F. By keeping temperatures stable, the beer maintains its intended flavor profile and volumes of CO2, ensuring a satisfying experience with every glass.
Optimizing Kegerator Settings and Beer Line Length
When using a kegerator, optimizing settings helps achieve the perfect pour. This includes setting the correct temperature and adjusting CO2 pressure appropriately. It's important to balance these elements to avoid issues like over-carbonation or flat beer.
To achieve this, it might be necessary to use secondary regulators, which control the gas pressure used to push beer from the keg. This ensures the beer flows smoothly without excessive foaming or overly rapid pouring. Regularly checking and fine-tuning both the temperature and pressure settings in a kegerator not only preserves beer quality but also prolongs the lifespan of the equipment.
Understanding how to manage these components can save both time and product loss, making it essential for any serious beer enthusiast or homebrewer.
Keg Components and Materials
Keg systems use specific materials for safety and efficiency. 304 stainless steel and various fittings, like quick disconnects, play key roles. Understanding these can improve system performance.
Advantages of 304 Stainless Steel
304 stainless steel is a top choice for keg systems due to its durability and resistance to corrosion. This material withstands various temperature changes without compromising structural integrity. It is easy to clean, which is crucial for maintaining hygiene in beer dispensing systems.
Stainless steel ensures that flavors remain pure, preventing any metallic taste from leaching into the beverage. Additionally, it is rated to handle the pressure ranges commonly required in draft systems, offering a safe and reliable solution for beer storage and dispensing.
Selecting Fittings and Connectors
Choosing the right fittings and connectors is vital for a seamless keg setup. One popular option is the quick disconnect, which allows for easy connections and disconnections without the need for tools. This feature is especially useful for switching between different kegs quickly and efficiently.
When selecting fittings, it's important to ensure compatibility with the materials used in the keg system to prevent leaks. Stainless steel fittings are often recommended for their strength and rust resistance. Proper selection enhances flow rate and maintains a secure system, keeping pressure consistent and minimizing the risk of malfunction during operation.
Carbonation Techniques
Carbonation in kegs can be achieved using methods like force carbonation and natural carbonation. Both techniques involve different approaches with distinct benefits, catering to various preferences for CO2 levels and ease of use.
Force Carbonation Method
Force carbonation is a popular technique for quickly carbonating beer in a keg. This method involves using a carbon dioxide (CO2) tank to infuse the beverage. By setting a higher carbonation pressure, typically between 30-45 psi, beer absorbs CO2 more quickly. This process takes just a few days or even hours, depending on the desired carbonation level.
Homebrewers often prefer this method for its speed and control over carbonation levels. For instance, the quick shake method involves shaking the keg at higher psi to carbonate the beer faster. Once the desired carbonation is reached, the pressure is reduced to serving levels, usually around 12-14 psi. This ensures that the beer is consistently carbonated and ready to be served promptly.
Natural Carbonation Prospects
Natural carbonation provides a softer, smoother mouthfeel compared to force carbonation. For brewers interested in a traditional method, this is an appealing option. Though it requires patience, the resulting taste and texture can be quite satisfying. Additionally, some brewers feel that natural carbonation brings out more depth in flavor. Using this method requires more monitoring to avoid over-carbonation, but it offers a unique way to enhance the final product's character.
Cleaning and Maintenance
Proper keg cleaning and maintenance ensure the beer remains fresh and safe to drink. Regular cleaning, sanitizing, and inspection help prevent the buildup of residues, bacteria, and potential damage.
Sanitizing Your Keg
Sanitizing is essential to keep kegs free from bacteria and unwanted residues. Start by rinsing the inside of the keg with warm water to remove any remaining beer or particles. Then, apply a cleaning solution, such as a caustic wash, which is effective at cleaning both keg surfaces and valve stems. Follow with an acid solution wash to neutralize any chemical residue and provide an extra level of cleanliness.
It's important to use materials suitable for kegs, such as 304 stainless steel, which resists corrosion. For home brewers, using a quick disconnect can make connecting cleaning lines easier and more efficient. This ensures no leftover contaminants remain in the keg that could affect the keg pressure or the taste of the beer.
Regular Keg Inspection
Conducting regular keg inspections helps identify wear and tear early. Check all seals and gaskets for cracks or damage, as these can affect keg pressure and lead to leaks. Inspect the outside and inside of the keg for dents or signs of corrosion, especially if they are frequently moved or stored in damp environments.
Pay special attention to the valve systems, ensuring they are clean and functioning properly. Regular maintenance of keg components, particularly those made from 304 stainless steel, ensures long-term durability and performance. Regular inspections prevent unexpected keg failures, which could disrupt service.
Troubleshooting Common Issues
When dealing with keg pressure problems, it's important to address potential leaks and manage carbonation levels. These key points ensure that the beer is served as intended, with the right fizz and without waste.
Dealing With Leaks
Leaks can lead to pressure loss and wasted CO2. Start by checking all seals and connections, as they are the most likely culprits. Applying a solution of water and dish soap to seams can help identify leaks by producing bubbles where CO2 escapes. The pressure relief valve should be checked for proper operation to ensure it isn’t venting gas unnecessarily. If a leak is found, tighten connections or replace worn parts like o-rings or seals. A consistent psi setting is critical, so verify it with a reliable gauge to maintain correct pressure levels.
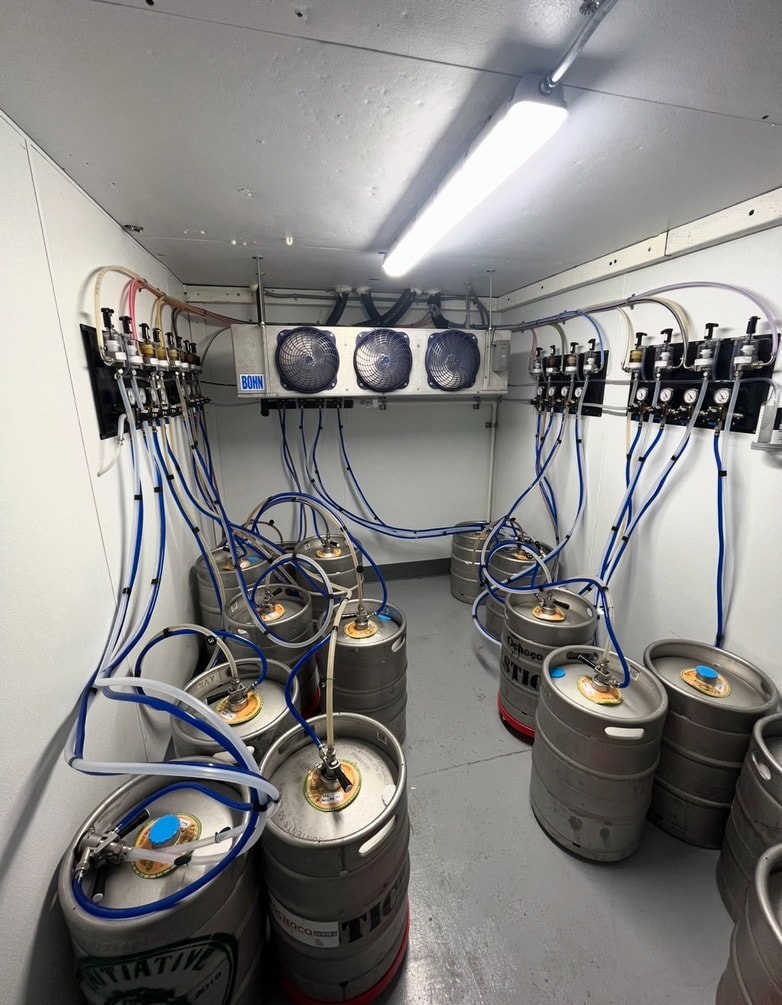
Managing Over/Under Carbonation
Over or under carbonation affects beer taste and presentation. For under-carbonated beer, increase the psi, but do it gradually to avoid over-correction. Ideal serving pressure often ranges around 12-14 psi, but this can vary based on the beer style. Use a CO2 tank that is full and functional. If the beer is over-carbonated, reduce the pressure carefully and allow the keg to settle. The beer should have the right volumes of CO2, typically between 2.2 and 2.5 volumes, depending on the style. Always give the system time to stabilize after adjustments to avoid repeated issues.
Frequently Asked Questions
When dealing with keg pressure, various factors like beer style and carbonation levels play crucial roles in determining the correct settings. Understanding these elements ensures that the beer is served with the best taste and quality.
What is the ideal CO2 pressure for serving different styles of beer?
Different beer styles require varying CO2 pressures. For instance, wheat beers, Belgian beers, and American sours are highly carbonated and typically need CO2 pressures of about 15 to 20 psi.
How do you calculate the correct serving pressure for a keg?
To calculate serving pressure, consider factors like the beer style, temperature, and length of the beer line. It's essential to balance these variables to maintain the desired carbonation and flow rate.
At what PSI should a CO2 tank be set to maintain optimal carbonation for beer?
Most CO2 draft beer systems perform well around 12-14 psi, depending on the system design and beer temperature. This setting helps achieve proper carbonation and maintains beer quality. This also depends on the type of beer system and how long the beer runs from cooler to tap.
Can excessive pressure affect the quality of beer from a keg?
Excessive pressure can lead to over-carbonation, causing the beer to pour with too much foam and affecting taste. It's crucial to maintain the correct pressure to ensure that the beer's texture and flavor remain intact.
What are the recommended CO2 pressure settings for an IPA?
IPAs usually require a slightly lower CO2 pressure compared to more carbonated beer styles. The pressure should be adjusted for the specific IPA being served to maintain its unique balance of hops and malts.
How does the type of beer influence the required keg PSI for serving?
Beer style influences the required keg PSI significantly. For example, lighter beers with higher carbonation levels, like sours, need higher pressure than heavier beers such as stouts. Adjusting the PSI based on beer type ensures optimal pouring and taste.
Summary
Keg pressure plays a crucial role in maintaining the right carbonation and flow of draft beer. It's essential for ensuring the best taste and presentation of beverages.
To achieve the right pressure, factors such as temperature, type of beer, and altitude need consideration. For instance, keg pressure often ranges depending on these factors.
Examples of Pressure Levels:
- Stout Beers: Typically served at lower pressures.
- Lighter Beers: Might require higher pressure levels for optimal carbonation.
It's also important to be aware of the equipment settings, such as the CO2 regulator. Adjusting the regulator knob clockwise increases pressure while counterclockwise reduces it.
Useful tools can include a pressure monitor gauge, which helps maintain the desired pressure level. Additionally, elevation can affect the pressure setting due to atmospheric changes.
Correctly understanding and managing keg pressure ensures consistent quality and satisfaction for beer enthusiasts.