Glycol to Water Ratio Glycol Chiller Draft Beer: Optimal Cooling Efficiency
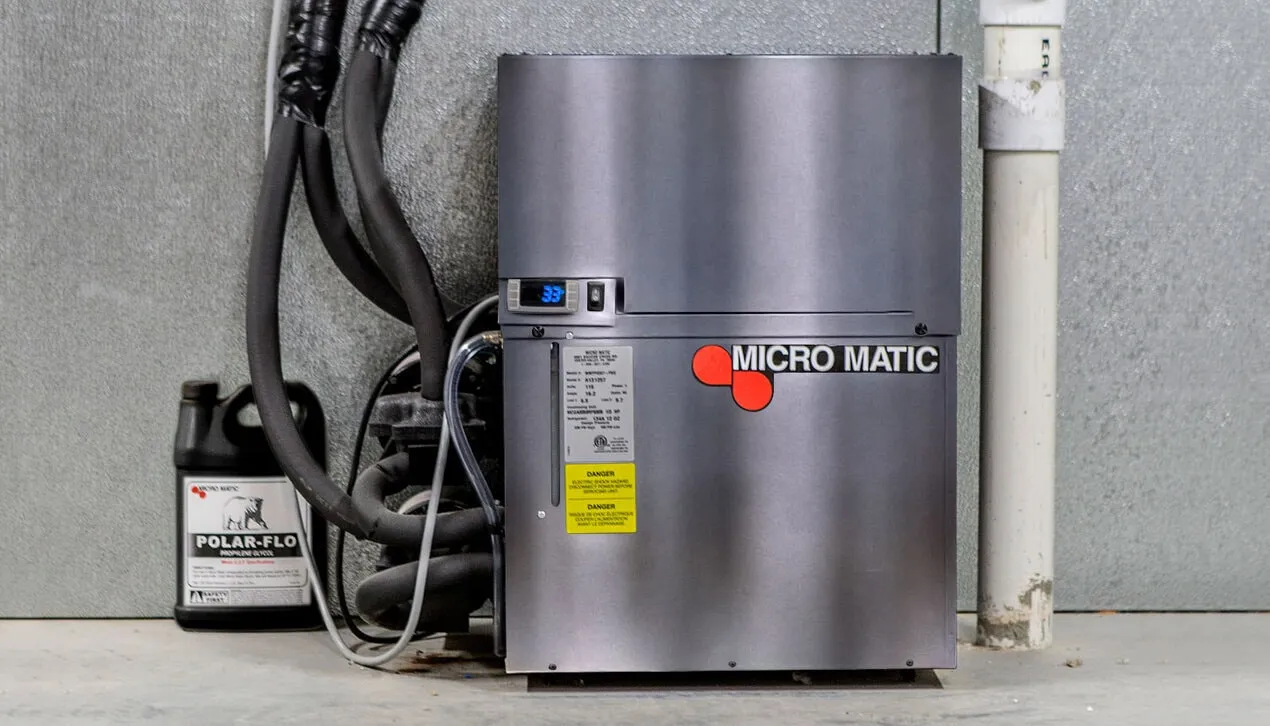
Anyone interested in serving the perfect draft beer must understand the role of glycol chillers. These systems keep your beer at an ideal temperature from the keg to the glass. The recommended glycol-to-water ratio in these chillers is typically 35% to 40%, which is considered the best ratio for ensuring efficient cooling without being too thick to pump. This balance is crucial to maintaining the right consistency and flow through the system.
Unlike other cooling methods, glycol chillers offer precise temperature control, which is crucial for maintaining beer quality. They work by moving a chilled mixture through lines that run parallel to the beer lines, keeping everything cold. This helps preserve the taste and aroma of craft beers, making them a popular choice among breweries.
Choosing the proper setup includes designing a system that meets specific needs regarding range and capacity. Regular maintenance and correct installation are also essential to ensure operational efficiency and reduce the chance of problems. Craft beer fans and bar owners can significantly benefit from using a proper glycol chiller setup. Understanding this will enhance both the enjoyment of beer and the efficiency of the draft system.
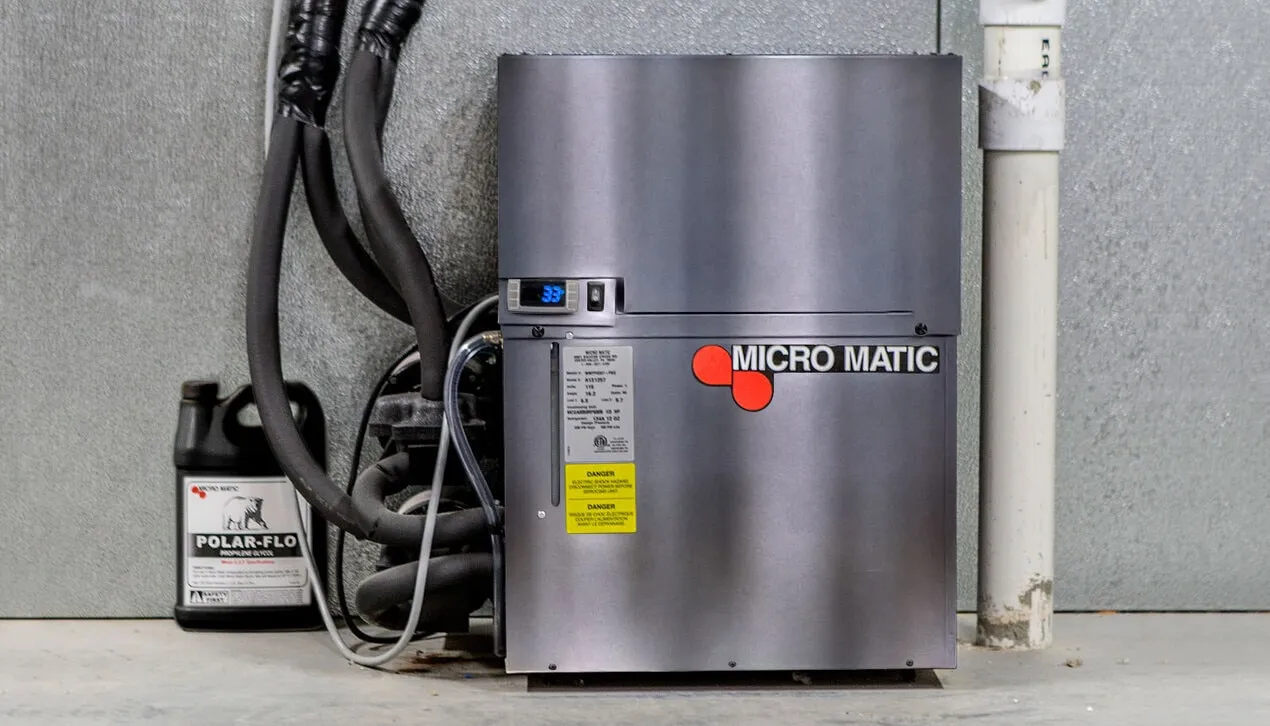
Key Takeaways
- Glycol chillers maintain beer temperature with a 35%-40% glycol ratio.
- They ensure precise temperature control for better beer quality.
- Regular maintenance is vital for efficient draft beer systems.
Understanding Propylene Glycol in Draft Beer Systems
Glycol is a key component in draft beer systems. It is used in various forms, including propylene glycol and ethylene glycol. Propylene glycol is often the choice due to its lower toxicity and suitability for food-related applications.
Draft beer systems rely on glycol chillers to keep beer at the ideal temperature from the cooler to the tap. These systems often include a glycol reservoir that holds a mixture of glycol and water. This mixture is pumped through beer lines to maintain cold temperatures.
The typical mixture in these systems is a 35% to 40% glycol-to-water ratio. Determining how much glycol is needed is crucial for achieving the correct water-to-glycol mix ratio for effective cooling. This balance ensures the mixture is not too thick to pump or too thin to provide sufficient cooling. The use of inhibited USP-grade propylene glycol ensures both safety and efficiency.
A glycol system may include components like a glycol power pack, which helps maintain the chilled state. Such systems are essential in long-draw draft beer setups, where precise temperature control is necessary. Efficient glycol cooling allows for consistent quality and taste of beer served.
Using food-grade propylene glycol is advisable for brewery operations. This ensures compliance with health standards. Understanding these components and how they work together is crucial for anyone maintaining or operating a glycol beer system.
The Role of Glycol Chillers in Maintaining Beer Quality
Glycol chillers are critical to maintaining high beer quality. They ensure precise temperature control from keg to tap. The glycol mixture also helps raise the coolant's boiling point, allowing the system to operate efficiently without overheating. A glycol beer chiller system circulates a mixture of glycol and water to effectively cool the beer lines.
The right glycol/water ratio ensures proper chiller efficiency. Typically, a mix of 35% to 40% glycol keeps the system cool without making it difficult to pump. This ratio helps maintain the desired texture and taste of the beer.
These chillers use a glycol trunk line to keep the beer at an optimal temperature. This ensures consistent chilling, which is crucial for flavor. The system also prevents hot spots that could damage the beer’s delicate balance.
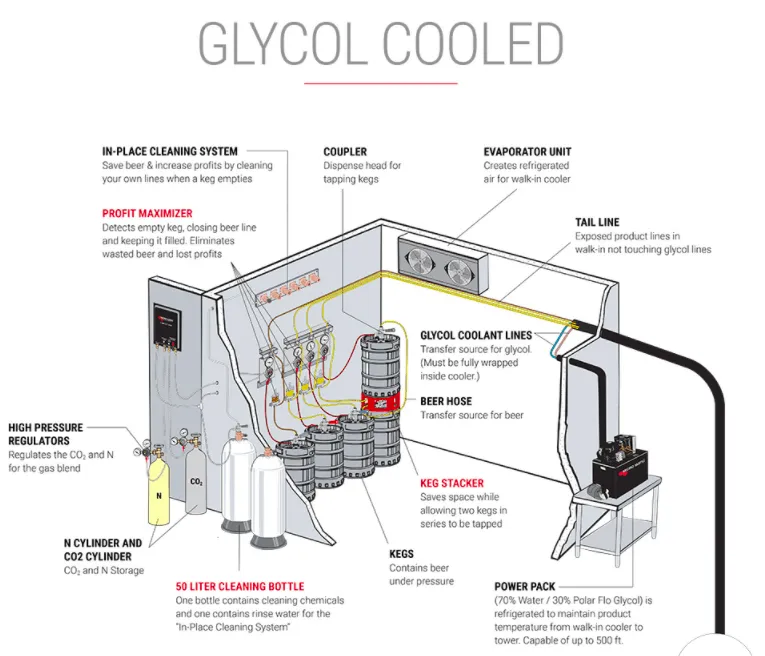
Glycol cooling systems are standard in breweries. They handle the needs of both large and small operations. By maintaining consistent temperatures, they protect the beer’s integrity and ensure a satisfying experience for any beer enthusiast.
Employing a good glycol chiller ensures high-quality beer is always on tap, offering reliable performance. These systems are an essential part of any establishment that prioritizes beer quality. Whether for a bar, restaurant, or brewery, these chillers maintain the correct environment for each pour.
Design and Components of Glycol Draft Beer Systems
A glycol draft beer system keeps beer at the perfect temperature from the keg to the glass. These systems are essential in maintaining flavor and quality.
Key components include the glycol power pack, which is the heart of the cooling process. It contains a chiller that cools the glycol-water mixture. This mixture is then circulated through the system to ensure the beer stays cold.
The trunk line plays a critical role in this system. It consists of both glycol lines and insulated beer lines. The glycol lines transport the chilled glycol mixture, while insulated beer lines carry the beer from the kegs to the dispensing point.
Beer towers are located in the dispensing area. They are connected to the beer lines and ensure that beer is served at the right temperature. Different styles of beer towers are available to suit various bar designs.
In a long-draw system, maintaining a proper glycol-to-water ratio is important. Typically, this is around 35% to 40% glycol since it ensures effective cooling. This mix travels smoothly through glycol piping without freezing.
Regular maintenance of glycol cooling systems is crucial. Cleaning the beer lines and checking that the glycol chiller functions well are necessary steps for optimal performance. This upkeep ensures that the beer quality is never compromised while keeping costs down.
Using corrosion inhibitors in the glycol mixture can help prevent rust and corrosion in the system, ensuring long-term durability.
Understanding these components helps troubleshoot and optimize the efficiency of glycol draft beer systems.
Installation and Maintenance Considerations
Installing a glycol chiller system for draft beer involves several components. Contractors often use Schedule 80 PVC or cross-linked polyethylene (PEX) for piping. These materials ensure durability and effective cooling performance. Proper installation is crucial to maintain the optimal temperature differential between the walk-in cooler and the beer dispensing area.
Key components in the installation process include the refrigeration system, heat exchanger, and keg coupler. Each part must be correctly calibrated to ensure efficient operation. When selecting a system, consider the layout of the bar or brewery to determine the best setup for efficient beer dispensing.
Maintenance of the glycol chiller system is essential for long-term performance. Regular checks should be performed to avoid any issues, such as glycol freezing point problems. Cleaning the beer lines and checking connections, including those at the keg coupler, helps maintain system efficiency.
Frequent inspections help identify issues like leaks or temperature fluctuations early on. Adjustments in the refrigeration system can prevent costly repairs and downtime. Partnering with a reputable service provider like Micro Matic can ensure that the system receives proper care.
Regular maintenance includes checking the glycol concentration and ensuring it remains at the recommended ratio. Regularly checking the glycol concentration is vital for ensuring adequate freeze protection during cold weather. This is vital for maintaining the right cooling performance and preventing the risk of freezing. Keeping the system in top condition maximizes the quality and efficiency of the beer dispensing system.
Operational Efficiency and Troubleshooting
Maintaining the right glycol-to-water ratio in a chiller is critical for operational efficiency. The glycol mixture's heat capacity plays a crucial role in its ability to absorb and transfer heat efficiently. A typical mixture is 35% glycol to 65% water, which protects the beer from freezing at around +1°F. This ensures that the system efficiently cools beer, preventing overheating and downtime.
Components like the compressor, condenser, and evaporator fan also impact efficiency. They work together to keep beer at the right temperature. When any part fails, it may lead to customer dissatisfaction due to foam or warm beer.
It is essential to monitor and adjust the ambient temperature accordingly. High ambient temperatures can stress the system, making the compressor work harder. This can increase the cost of production due to inefficient energy use.
Check the tank volume for the glycol solution regularly. A low level can cause issues with maintaining a cold draft beer temperature, leading to more foam and wasted product.
Troubleshooting involves ensuring each part functions well. Listen for unusual noises and feel for vibrations or excessive heat. These can be early signs of problems. Addressing them quickly will improve operational efficiency and prolong the life of the system.
Ensuring the system is foam-free also enhances customer satisfaction, as it prevents wastage and keeps pour costs low.
Frequently Asked Questions
Choosing the right glycol-to-water ratio is crucial for ensuring optimal performance in draft beer cooling systems. The liquid properties of the glycol mixture are essential for maintaining optimal temperatures in the cooling system. Understanding the effects of different glycol percentages and knowing how to troubleshoot common issues can help maintain the quality and consistency of beer.
How do I determine the correct glycol-to-water mixture for my draft beer system?
The ideal mixture for most systems is often around 35% to 40% glycol. This ratio ensures efficient cooling and prevents freezing. Consult the manufacturer's specifications for precise guidelines tailored to your specific setup.
What are the effects of glycol percentage variations in a chiller system for draft beer?
Too much glycol can lead to thicker solutions that reduce cooling efficiency, while too little may cause freezing. Using pure water can increase heat capacity, but it may not provide adequate freeze protection. Maintaining the recommended ratio helps achieve consistent temperatures and optimal system performance.
Can you provide a chart or guide for glycol-to-water ratios in beer cooling systems?
Industry charts specify ratios like 35% glycol to 65% water for standard operations. These charts provide quick reference points to ensure the correct mixtures for varying temperature requirements and chiller models.
How do you calculate the right amount of glycol needed for a draft beer cooling system?
First, determine the system's volume capacity. Multiply the total volume by the desired glycol percentage to find the specific amount of glycol needed. This ensures a balanced ratio that maintains optimum cooling efficiency.
What troubleshooting steps should be taken if a glycol beer system is not cooling properly?
Check for issues like ice formation or blocked condenser fins. Ensure ample airflow around the unit and verify glycol levels. Adjust the mixture if necessary and perform regular maintenance to keep the system running smoothly.
Summary
The glycol-to-water ratio is crucial for the efficient operation of glycol chillers in draft beer systems. Typically, the ideal mixture is 35% to 40% glycol to water, which ensures optimal cooling and prevents freezing.
Glycol acts as a cooling agent, keeping the beer at the right temperature from the keg to the tap. This mixture absorbs heat as it circulates through the system, maintaining a consistent beer temperature.
Propylene glycol is commonly used because it is safe and non-toxic, making it suitable for food and beverage applications. Its properties help prevent the beer from warming up and ensure a crisp taste when served.
With different components such as a reservoir, refrigeration system, and pump, glycol chillers operate in a closed-loop system. This setup keeps the glycol mixture moving efficiently, absorbing excess heat from the beer lines.
Using the proper glycol-to-water ratio is essential to avoid costly and disruptive issues like freeze-ups. A ratio of 35-40% inhibited propylene glycol is generally sufficient, even in colder climates.
Craft breweries rely on these systems to maintain the quality and taste of their product, ensuring every mug of draft beer is served perfectly chilled. The components of the glycol chiller work together efficiently to deliver this result.