Glycol Beer Systems: Ensuring Optimal Draft Beer Temperature Control
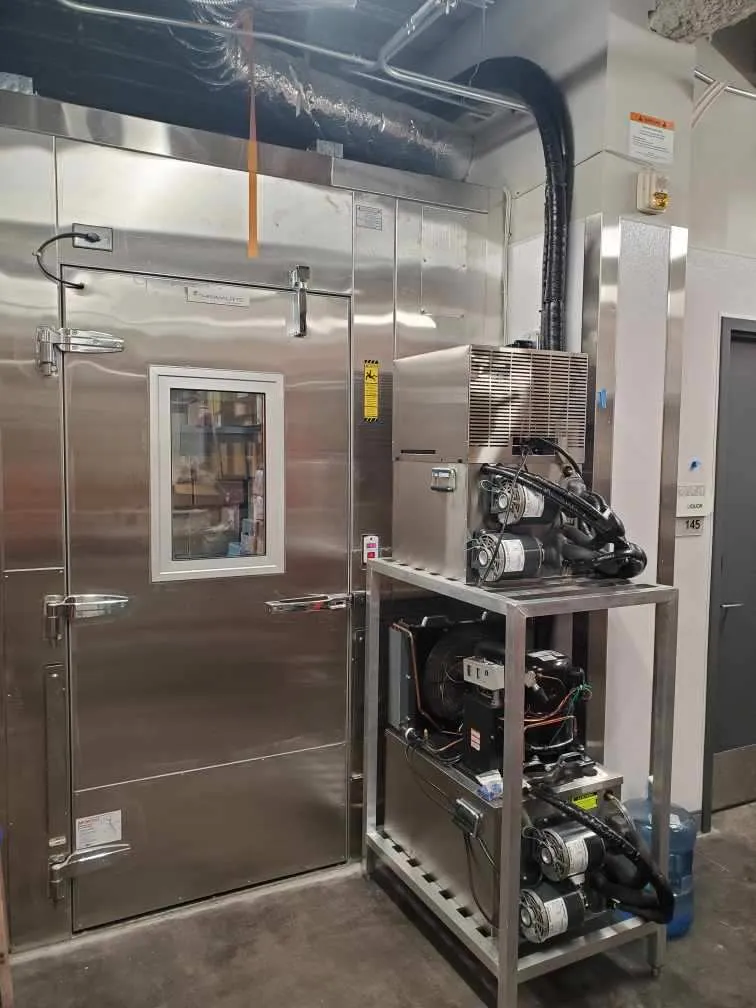
Glycol beer systems offer a technologically advanced method for retaining the freshness and ideal temperature of draft beer from keg to tap. These systems are particularly beneficial in establishments where there is a long distance between the beer kegs and the serving location, such as large bars or stadiums. The main component, propylene glycol, is a non-toxic, food-grade substance used for its chilling properties to ensure that the beer remains consistently cold during its journey through the lines.
The design and installation of a glycol beer system are critical to its efficiency and effectiveness. It requires a precise setup that includes a mixture of propylene glycol and water, known as a glycol bath, which circulates in lines adjacent to the beer lines. This helps maintain the optimal temperature for serving beer, typically around 38 degrees Fahrenheit. Continuous maintenance and operation are key to the longevity of the system, ensuring that every pint served is as intended by the brewer: crisp and refreshing.
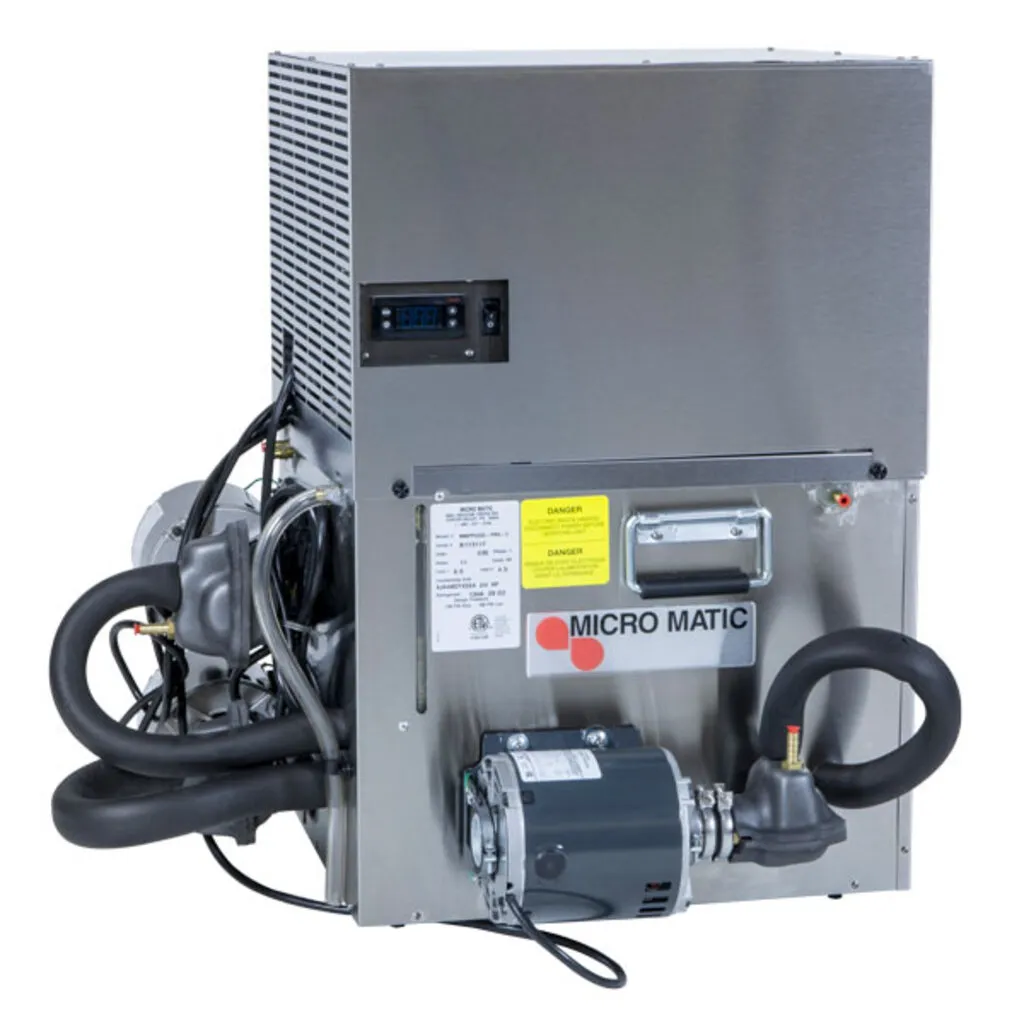
Key Takeaways
- Glycol beer systems use propylene glycol for optimal draft beer temperature.
- System reliability hinges on proper design, installation, and maintenance.
- Ensuring the freshness and quality of beer served over long distances.
Fundamentals of Glycol Beer Systems
Glycol beer systems are essential for maintaining the quality of draft beer through effective temperature control. These systems utilize glycol, a type of food-grade antifreeze, to provide consistent cooling for beer lines.
Basic Components and Functionality
Key components of a glycol beer system include a glycol chiller, glycol lines, and a glycol reservoir. The chiller cools a glycol mixture that is then circulated through the glycol lines encompassed in a glycol trunk line. This maintains beer at a consistent temperature from the keg to the tap.
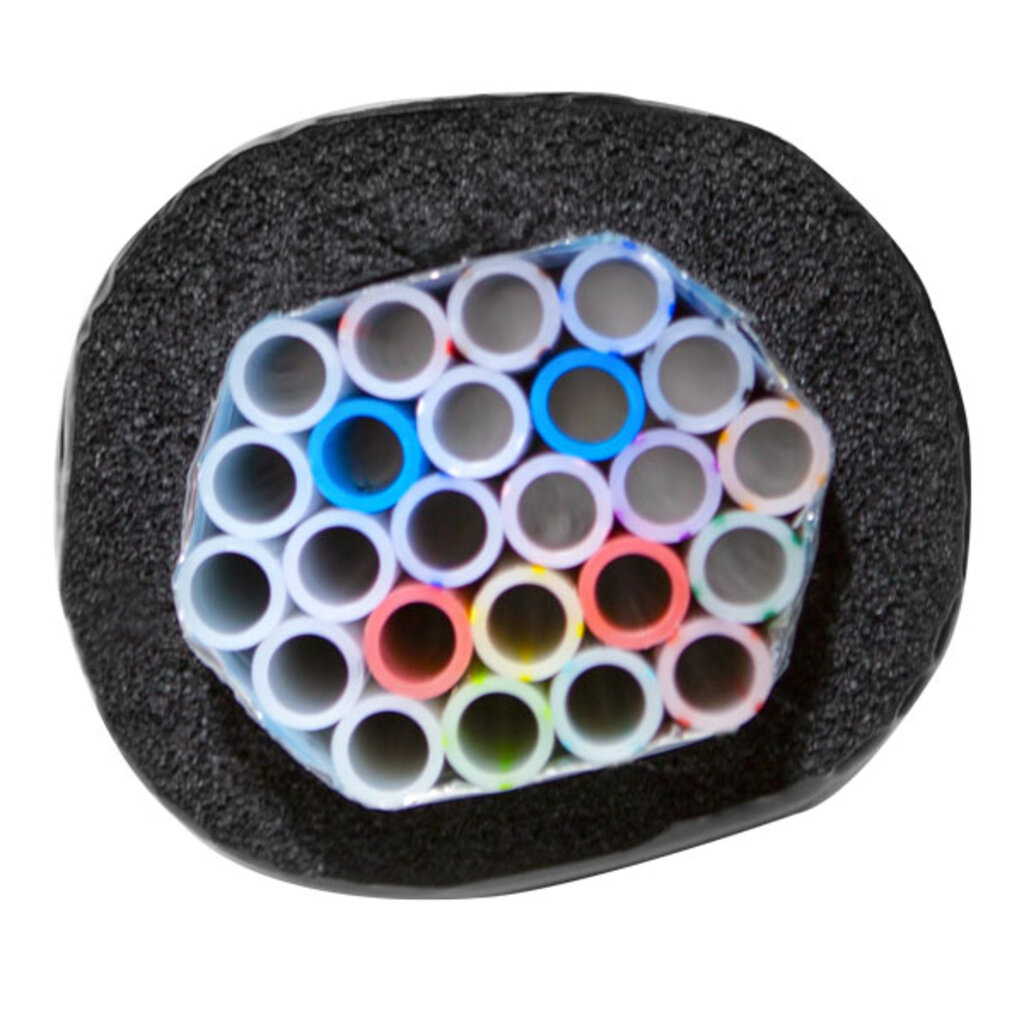
Types of Glycol Used
The primary type of glycol used is propylene glycol due to its low toxicity and classification as a food-grade antifreeze. Propylene glycol's properties prevent beer lines from freezing and ensure that drinks are dispensed at their optimal temperatures.
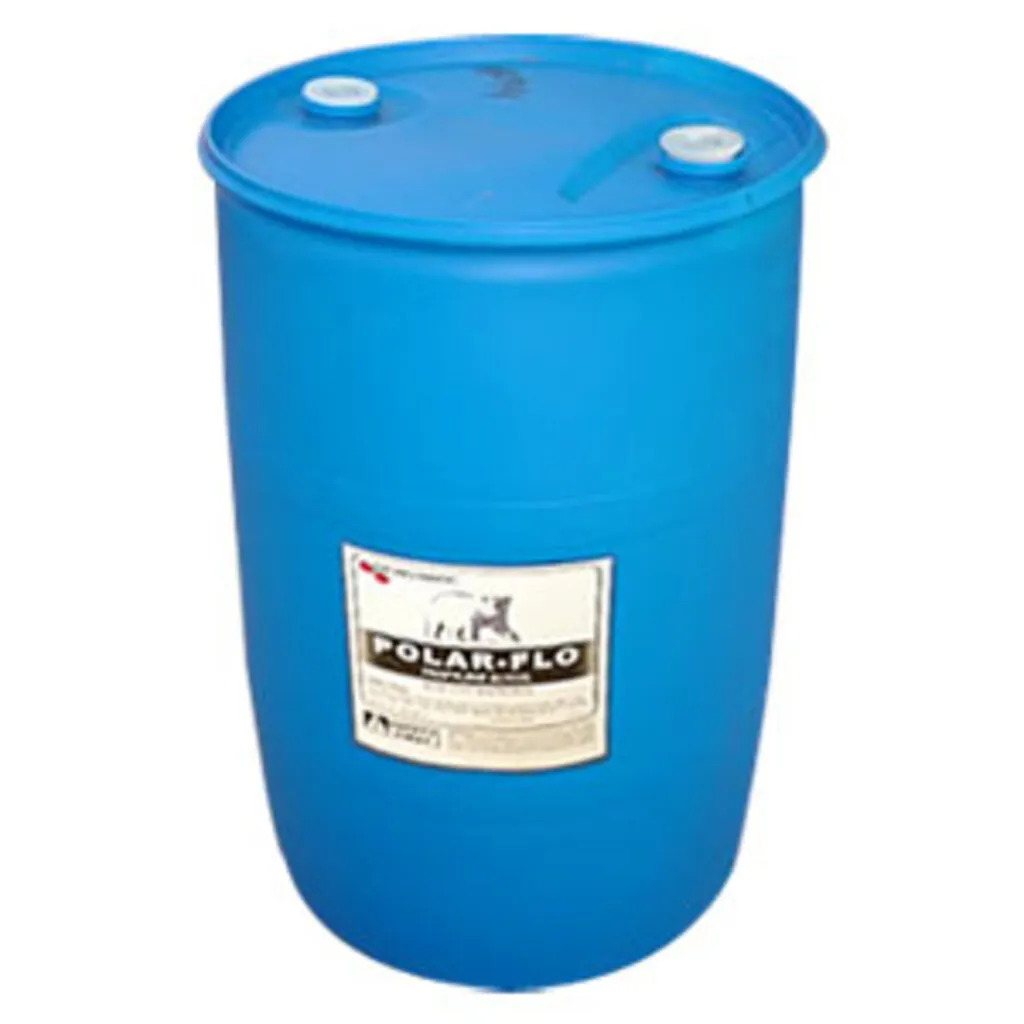
Types of Glycol Beer Systems
There are usually two main types of glycol systems found in establishments:
Air Cooled vs Water Cooled: Which is Better?
In a long-drawn draft beer system, the choice between an air-cooled glycol chiller and a water-cooled glycol chiller depends on several factors including efficiency, cost, installation requirements, and the environment where the system will be installed. Here's a comparison of both:
Air-Cooled Glycol Chiller
- Efficiency: Generally less efficient than water-cooled systems, especially in warmer climates. They rely on ambient air to dissipate heat, which can be less effective in hot environments.
- Cost: Typically less expensive to install than water-cooled systems. They do not require a water source or plumbing, which can reduce initial costs.
- Installation: Easier and less complex to install. They are ideal for locations where water access is limited or where additional plumbing would be impractical.
- Maintenance: Usually require more frequent maintenance, as they are exposed to environmental factors like dust and dirt which can clog the cooling fins.
- Environment Impact: More suitable for areas with cooler ambient temperatures. In hot climates, their efficiency drops significantly.
Water-Cooled Glycol Chiller
- Efficiency: More efficient than air-cooled systems, particularly in warm climates. They use water to dissipate heat, which is generally more effective than air.
- Cost: Higher initial installation cost due to the need for water lines and possibly a cooling tower or condenser.
- Installation: More complex installation process. Requires access to a continuous water supply and proper drainage, which can be a limitation in some areas.
- Maintenance: Typically require less maintenance than air-cooled systems, as they are not exposed to environmental debris.
- Environment Impact: Ideal for warm climates or environments where the ambient temperature is high. They are less affected by the surrounding temperature.
Conclusion
- Choose Air-Cooled: If you are in a cooler climate, have budget constraints, or face challenges with water access and plumbing.
- Choose Water-Cooled: If you are in a warmer climate or humid climate, can handle the higher initial cost and installation complexity, and have reliable access to water.
Remember, the specific needs of your establishment, including space constraints, local climate, and usage demands, should guide your decision. Consulting with a professional draft technician who understands the local conditions and requirements for draft beer systems can also provide valuable insights tailored to your situation.
System Design and Installation
Designing and installing a glycol beer system requires meticulous planning to ensure optimal functionality and efficient cooling. This includes carefully selecting and arranging components such as the compressor, glycol trunk line, and draft towers, as well as understanding the complexities of the installation process.
Layout and Planning
The layout phase is critical for a successful system. Engineers must calculate the distance between the kegs and the dispensing tower to determine the length of the trunk lines. The design should minimize the length of beer lines to ensure the beer remains cold and fresh from keg to tap handle. It is essential to include space for the compressor and motor, accounting for proper ventilation to maintain a consistent temperature. Draft beer equipment, including the keg coupler, shank, and faucets, must be precisely positioned to balance aesthetics with functionality.
Installation Process
The installation starts with setting up the draft beer system, which includes the positioning of the glycol lines and beer lines within the glycol trunk line – often a bundled configuration that keeps the beer at the correct temperature during transport. Technicians must secure the dispensing tower, ensuring the pumps and fan operate correctly to maintain consistent pressure and temperature. Each component, from the tap handle to the remote dispensing equipment, needs precise alignment and secure connections to prevent leaks and maintain quality.
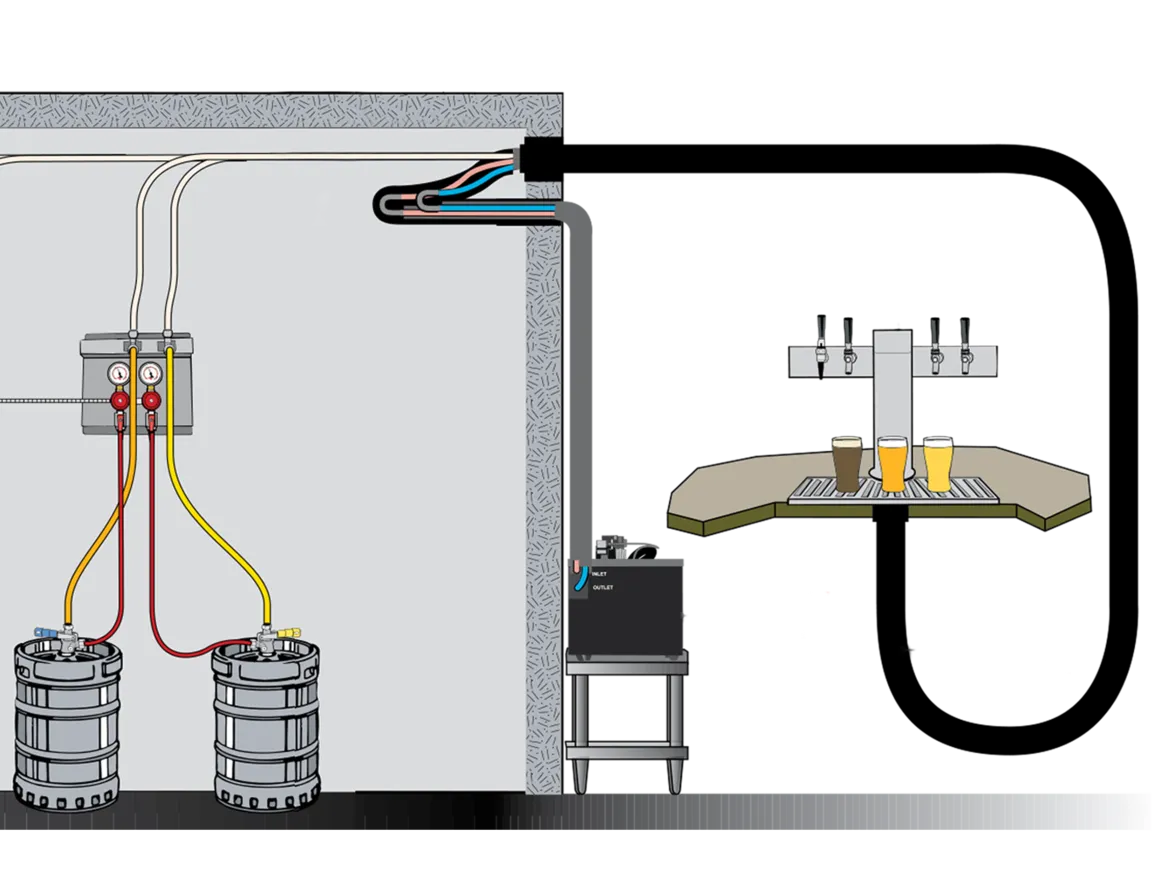
Can They Be Placed Inside a Beer Cooler?
Placing a glycol chiller for a draft beer system inside a cooler is generally not recommended for several reasons:
- Heat Generation: Glycol chillers generate heat as they operate. Placing one inside a cooler would counteract the cooler's purpose, as the chiller would raise the internal temperature, forcing the cooler to work harder to maintain its set temperature. This can lead to inefficiency and increased energy costs.
- Ventilation Requirements: Glycol chillers typically require proper ventilation to dissipate heat effectively. A cooler's enclosed space might not provide adequate ventilation, leading to overheating and potential damage to the chiller.
- Condensation and Humidity: The operation of a glycol chiller in a confined, cooler space can lead to increased humidity and condensation. This could potentially harm the chiller's components and also affect other items stored in the cooler.
- Space Constraints: Coolers are often limited in space and are designed to store kegs, bottles, and other refrigerated items. Adding a glycol chiller could create space constraints and disrupt the organization and accessibility of these items.
- Maintenance Access: Placing the chiller inside a cooler can make it more difficult to access for regular maintenance, repairs, or adjustments.
In summary, while it might seem convenient to place a glycol chiller inside a cooler, it's generally not advisable due to the potential for inefficiency, damage, and space issues. Proper placement and installation are key to ensuring the efficient and effective operation of your draft beer system.
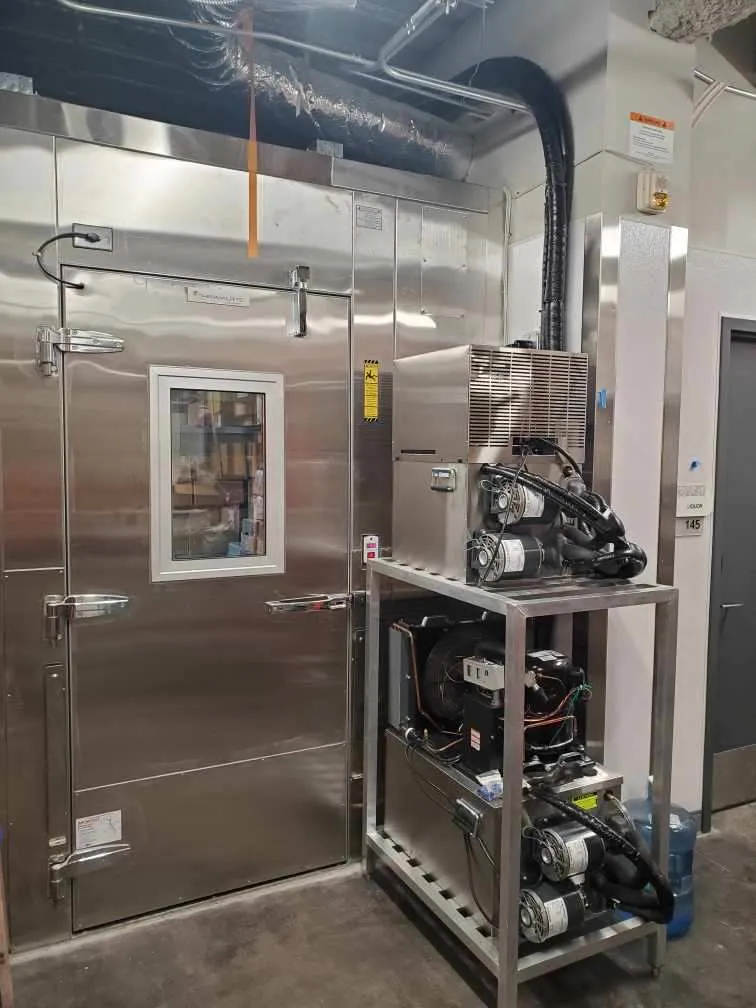
Operation and Maintenance
Glycol beer systems require meticulous attention to maintain proper temperature and ensure efficient operation. Regular maintenance of the refrigeration unit, cooling lines, and temperature controls is essential for delivering consistently chilled beer.
Maintaining Optimal Temperatures
Maintaining a consistent temperature is critical for glycol beer systems. Ideally, the beer temperature should be around 38°F to prevent foaming issues. A reliable refrigeration unit equipped with an evaporator fan and accurate thermostat is at the core of a glycol cooling system. For beers that require different storage conditions, such as nitrogenated beers, an adjustable gas blender or separator can be employed to balance the mix of CO2 and nitrogen gas, ensuring the beer's quality is preserved without temperature fluctuations affecting its integrity. Green Air Supply.
- Thermostat settings should be routinely checked to prevent temperature fluctuations.
- For cooling lines, a glycol power pack should be kept within the recommended temperature range.
- Component Optimal Temperature Range Beer temperature 36°F - 38°F Glycol bath 26°F - 29°F
Cleaning and Upkeep
Regular cleaning and upkeep of a glycol beer system are paramount. This not only includes the physical cleaning of components but also the glycol mixture itself and the internal parts of the system.
Maintaining a glycol chiller in a draft beer system is crucial for ensuring the system's efficiency, longevity, and the quality of the beer served. Regular maintenance helps prevent breakdowns, costly repairs, and downtime. Here's a general maintenance plan for glycol chillers:
Daily Maintenance
- Visual Inspection: Check for any signs of leaks, unusual noises, or vibrations.
- Temperature Monitoring: Ensure the chiller is maintaining the correct glycol temperature.
Weekly Maintenance
- Check Glycol Levels: Ensure the glycol reservoir is filled to the appropriate level. Low levels can indicate leaks or evaporation.
- Inspect Hoses and Connections: Look for any signs of wear, leaks, or loose connections.
Monthly Maintenance
- Clean Condenser Coils: Dust and debris can accumulate on the coils, reducing efficiency. Clean them with a coil cleaner or a soft brush.
- Check Glycol Quality: Test the glycol concentration and quality. Glycol can degrade over time and may need to be replaced or topped up.
- Inspect and Clean Fans and Vents: Ensure they are free of dust and debris for optimal airflow.
Annual Maintenance
- Comprehensive System Check: Conduct a thorough inspection of the entire system, including pumps, motors, and electrical connections.
- Replace Worn Parts: Any parts showing significant wear should be replaced.
- Glycol Replacement: Depending on the system's usage and glycol condition, an annual replacement may be advisable.
Regular maintenance of your glycol chiller is key to ensuring the quality of your draft beer and the reliability of your beer dispensing system. While some tasks can be handled in-house, others should be entrusted to professional technicians.
Advanced Considerations
When evaluating glycol beer systems, understanding advanced considerations is essential. These include troubleshooting common issues that may arise and recognizing potential costs and efficiency savings.
Troubleshooting Common Issues
A glycol beer system can experience various issues, primarily related to its refrigeration capabilities. Experienced operators should check for common problems in components like the glycol power pack. Issues could be a sign of antifreeze levels being too low, or the power pack could be malfunctioning, causing insufficient chilling. Routine checks should be performed on the beer tower and secondary regulators to ensure proper flow and temperature maintenance.
When dealing with suboptimal beer temperature or foam, examining the cooling agent consistency and supply and return lines for glycol beer systems is crucial. The system should maintain a consistent glycol-to-water ratio, typically between 35%-40%, to act as an effective antifreeze solution. Furthermore, maintaining the condenser and ensuring the air ducts are not compromised by blockage or leaks will enhance the efficiency of the refrigeration system.
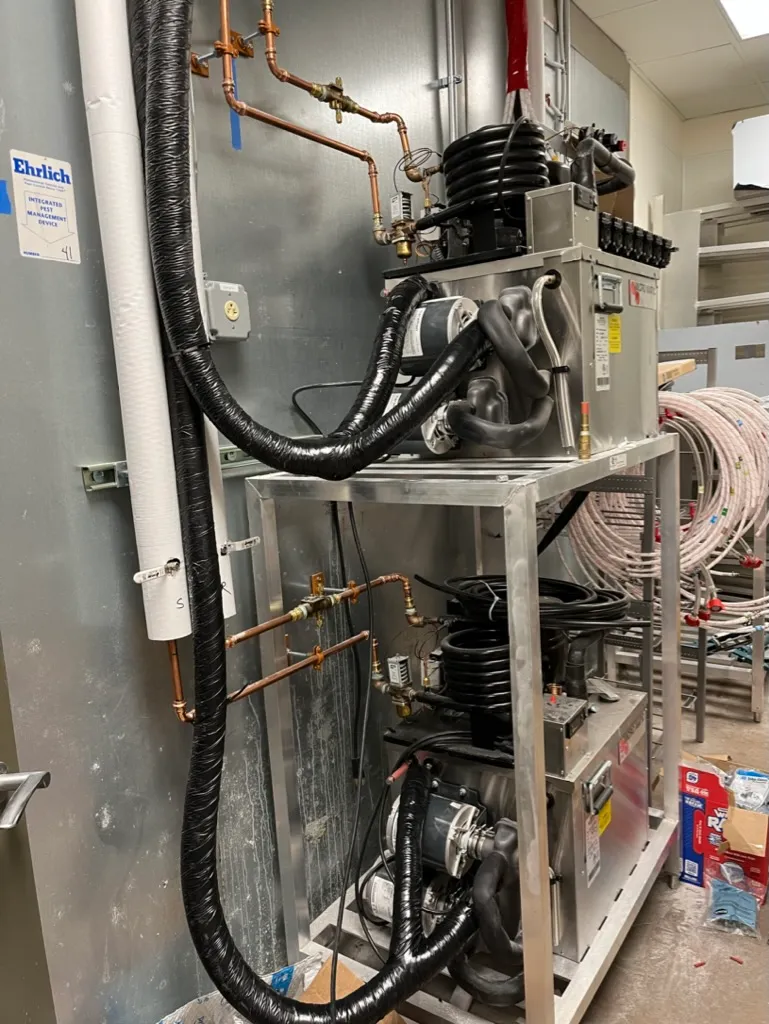
Costs and Efficiency Savings
Glycol beer systems, particularly those designed for long-draw dispensing, can be costlier due to their complexity and the premium components required for installation. The installation cost includes purchasing a high-quality glycol power pack, glycol, and components attached to the beer system designed for maintaining a variety of beers at optimal conditions.
Operators should evaluate the energy usage of their refrigeration system and the potential savings garnered from efficiency. Innovative elements like foil wrap surrounding supply and return lines contribute to maintaining the desired temperature over long distances, preventing heat gain, and reducing the load on the power pack. Upfront investments in components sourced from trusted manufacturers like Micro Matic can lead to a more reliable and cost-effective system over time.
Frequently Asked Questions
In this section, you'll find detailed answers to common inquiries about glycol beer systems. Whether you're considering installation or simply seeking to optimize your current system, these insights will help clarify your understanding.
What Factors Determine The Cost of Installing a Glycol Chiller System For Beer Dispensing?
The cost of installing a glycol chiller system is influenced by the size and scale of the system, the length of the beer lines, the number of taps being served, and the complexity of the installation. Prices also vary based on the quality of materials and specific contractor rates.
How Does a Glycol Draft System Maintain The Temperature of Beer?
A glycol draft system circulates a mixture of propylene glycol and water, known as a glycol bath, through lines that run parallel to the beer lines. This consistent chilling effect maintains the beer at an optimal temperature from the keg to the tap.
What Are The Advantages of Using a Glycol System Over Other Beer Cooling Methods?
Using a glycol system offers several benefits, including the ability to maintain consistent temperatures over long distances, making it ideal for establishments. Additionally, glycol systems prevent temperature fluctuations that can affect beer quality and pouring efficiency.
Can a Glycol Beer System Be Customized to Fit The Specific Needs of a Bar or Restaurant?
Customization is a key feature of glycol beer chiller systems. They can be tailored to fit the specific requirements of a venue, regarding the number of taps, cooling capacity, and layout constraints.
Summary
Glycol beer systems are essential in maintaining a constant and optimal temperature for draft beer from keg to tap. They utilize a mixture of glycol and water, regulated by a refrigeration unit, to cool the beer lines. This ensures that draft beer is served at the perfect temperature, enhancing the customer's experience.
- Function: Primary cooling system for long-draw beer dispensing
- Components: Glycol chiller unit, insulated beer lines, glycol/water mixture
The systems are highly efficient for venues like bars and restaurants where the distance between the keg and the serving station is significant. Glycol systems are particularly beneficial for establishments looking to serve beer far from the cooler or have multiple serving stations using one consolidated beer cooler.
Advantages:
- Consistency in beer temperature
- Versatility in setup (distance and location)
- Quality control over the serving temperature of beer
An important aspect of glycol systems is the substance glycol itself, which acts as an effective antifreeze, allowing the chilling system to maintain low temperatures without freezing the beer lines. It is a critical component for sustaining the quality and taste of the draft beer.
Considerations:
- Cost and installation complexity
- Maintenance requirements
- Energy efficiency
When selecting a glycol system, one must consider both the upfront costs and ongoing maintenance. Each component, from the chiller to the tubing, plays a significant role in the overall functionality and reliability of the system. Properly implemented, glycol beer systems are integral to serving draft beer at its highest quality.