Understanding Draft System Dynamics: The Beer Line Restriction Chart
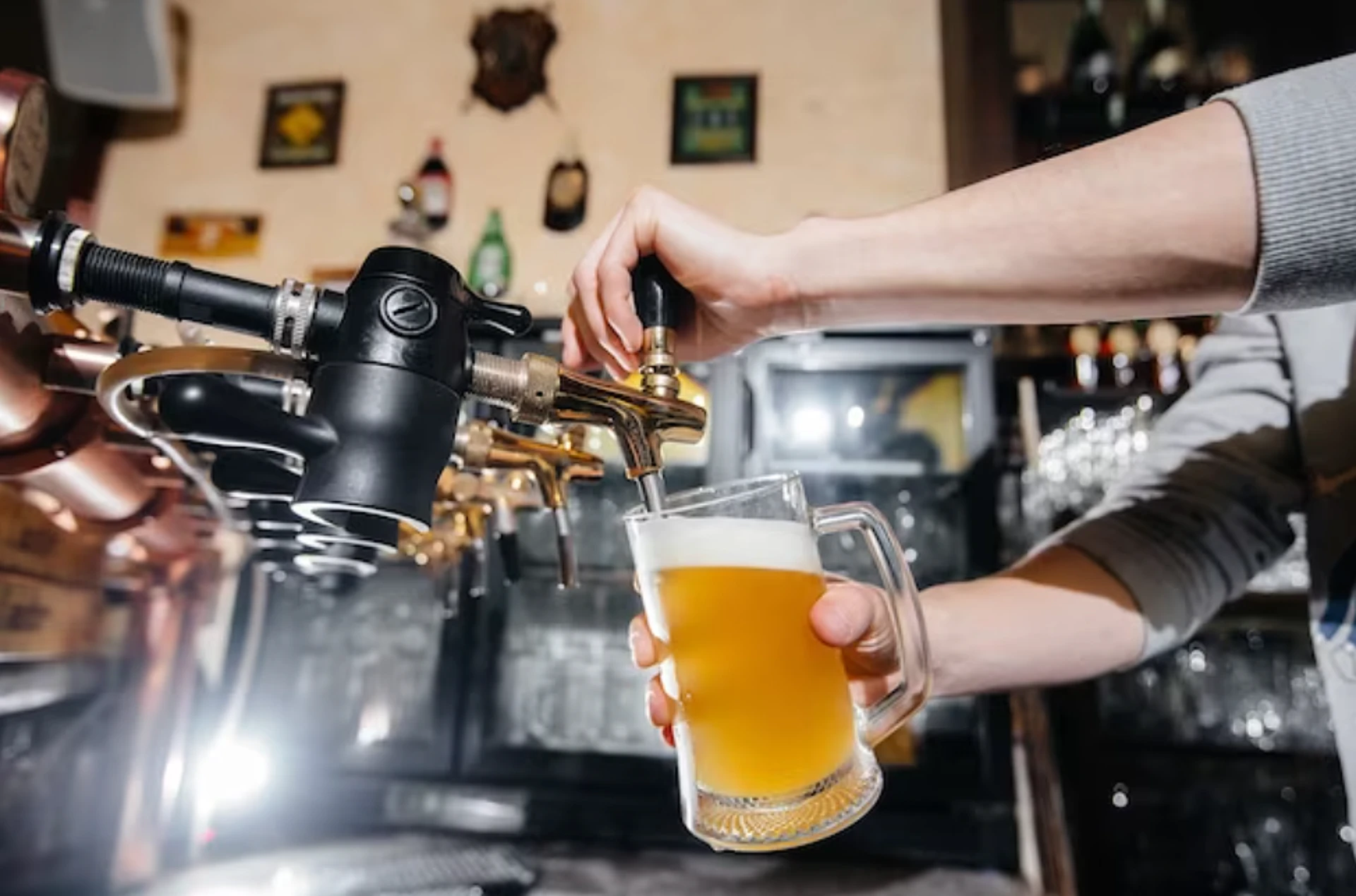
When setting up a draught beer system, controlling the flow of beer is crucial in order to achieve a perfect pour. Beer line restriction refers to the resistance within the beer lines that slows down the beer flow from the keg to the faucet.
Key Aspects:
- Line Diameter: Smaller lines have more resistance, impacting flow rate.
- Line Length: Longer lengths add more restriction, which can be calculated using a beer line calculator. The ideal pressure settings for draft beer systems can be determined by considering the 'feet x line resistance'.
- Material and Internal Texture: Different materials and textures contribute varying levels of friction.
- Elevation Change: Vertical distance from the keg to the tap affects gravitational pull and pressure.
Typical Restriction Values:
To serve beer with optimal carbonation and no excessive foam, the system’s pressure must balance with the inherent resistance offered by the beer lines. This equilibrium ensures a consistent flow rate and maintains the quality of the beer. Understanding the line resistance can lead to precise adjustments for a better beer dispensing experience.
Understanding Draft Beer Systems
A draft beer system is a network of components that work together to dispense beer from a keg to a faucet. The system consists of several key elements: a keg, a regulator, a beer line, a faucet, and a gas system. Each component plays a crucial role in ensuring that the beer is delivered with the right carbonation, temperature, and flow rate.
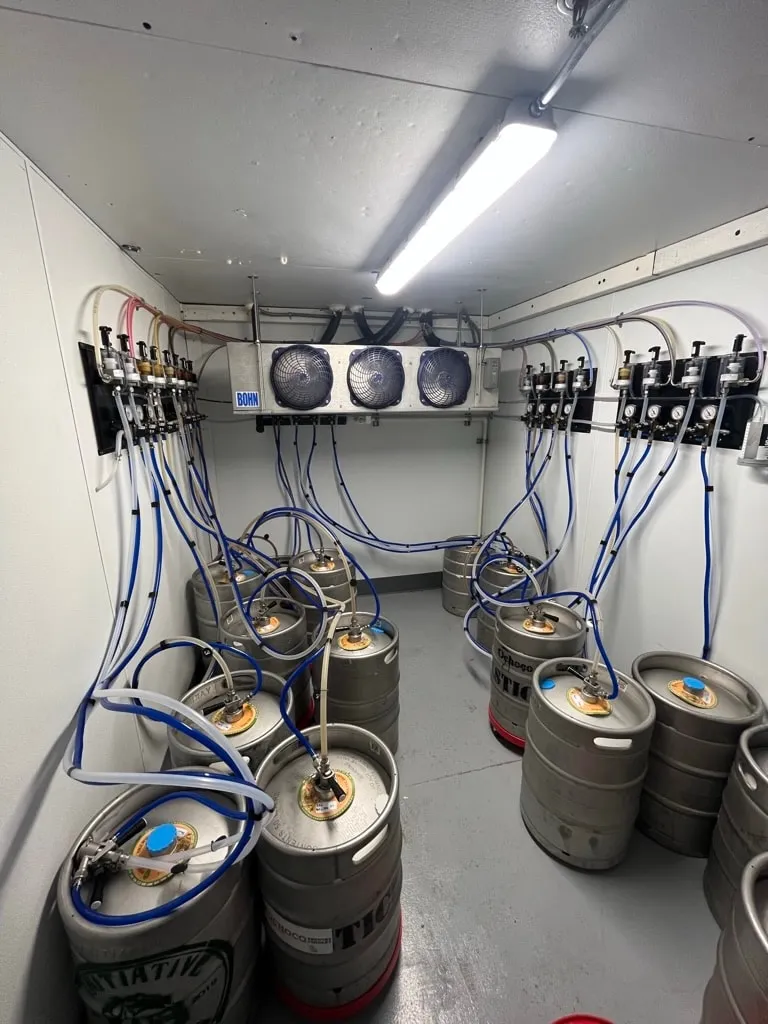
There are two main types of draft beer systems: direct draw and long-draw systems. In a direct draw system, the keg is located near the faucet, typically within a few feet. This setup is common in home draft systems and small bars where space is limited. Direct draw systems are relatively simple to set up and maintain, making them a popular choice for those new to draft beer systems.
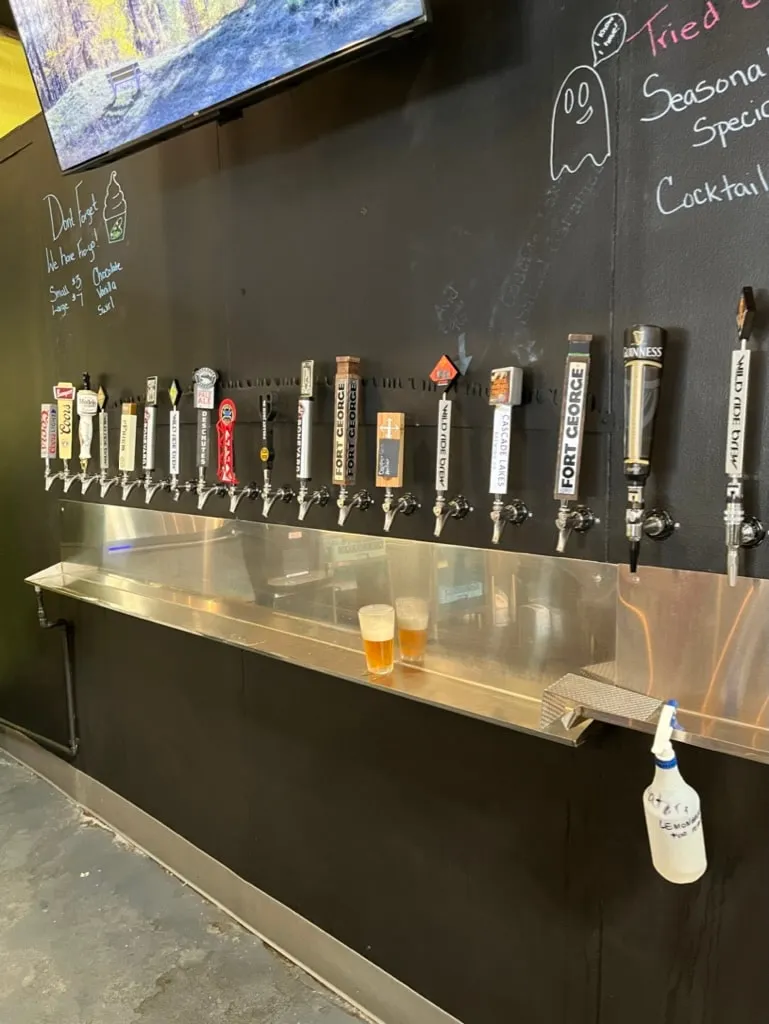
On the other hand, long-draw systems are used in larger establishments where the keg is located farther away from the faucet. These systems often use glycol cooling to maintain the beer’s temperature over longer distances. Long-draw systems are more complex and require precise calibration to ensure the beer is dispensed correctly.
Understanding how these components interact is crucial for maintaining a well-balanced system that delivers high-quality beer. Whether you are using a direct draw or long-draw system, knowing the ins and outs of your draft beer system will help you achieve the perfect pour every time.
Beer Line Restriction Explained
Beer line restriction refers to the resistance that beer lines provide against the flow of beer. This resistance is caused by the friction between the beer and the inner surface of the beer line. The level of restriction depends on several factors, including the type of beer line used, its length, and its internal diameter.
A higher restriction value means that the beer line provides more resistance to the flow of beer. This can affect the serving pressure and the overall performance of the draft beer system. For instance, a longer beer line or one with a smaller internal diameter will have a higher restriction value, requiring adjustments in the system’s pressure settings to maintain a balanced flow.
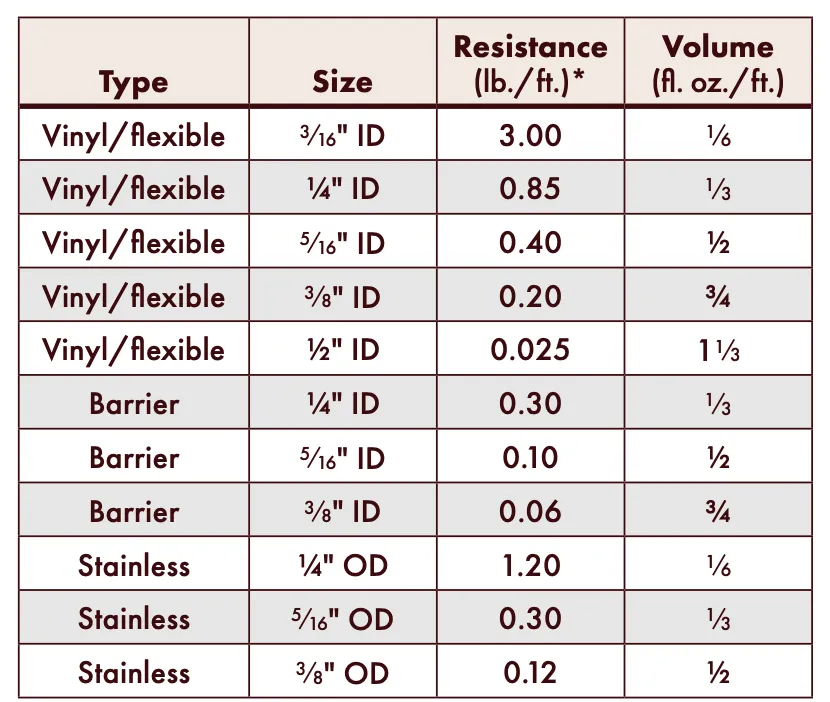
Different materials used for beer lines also contribute to varying levels of restriction. Stainless steel beer lines, for example, are known for their durability and cleanliness but have higher resistance compared to vinyl lines. Understanding these nuances helps in selecting the right beer line for your system and making necessary adjustments to achieve optimal performance.
By carefully considering the restriction value of your beer lines, you can ensure that your draft beer system operates smoothly, delivering beer with the right carbonation and flow rate.
Variation in Resistance Among Beer Line Types
When setting up a draft beer system, the inner workings are not visible to customers, but these components are crucial for a proper draft beer dispensing system. A fundamental aspect of this setup is understanding that different materials used for beer lines can have varying levels of resistance or Line Resistance values.
- Stainless Steel Lines: Known for their durability and cleanliness, stainless steel lines present a higher resistance and are often used in long-draw systems due to their ability not to affect beer's taste.
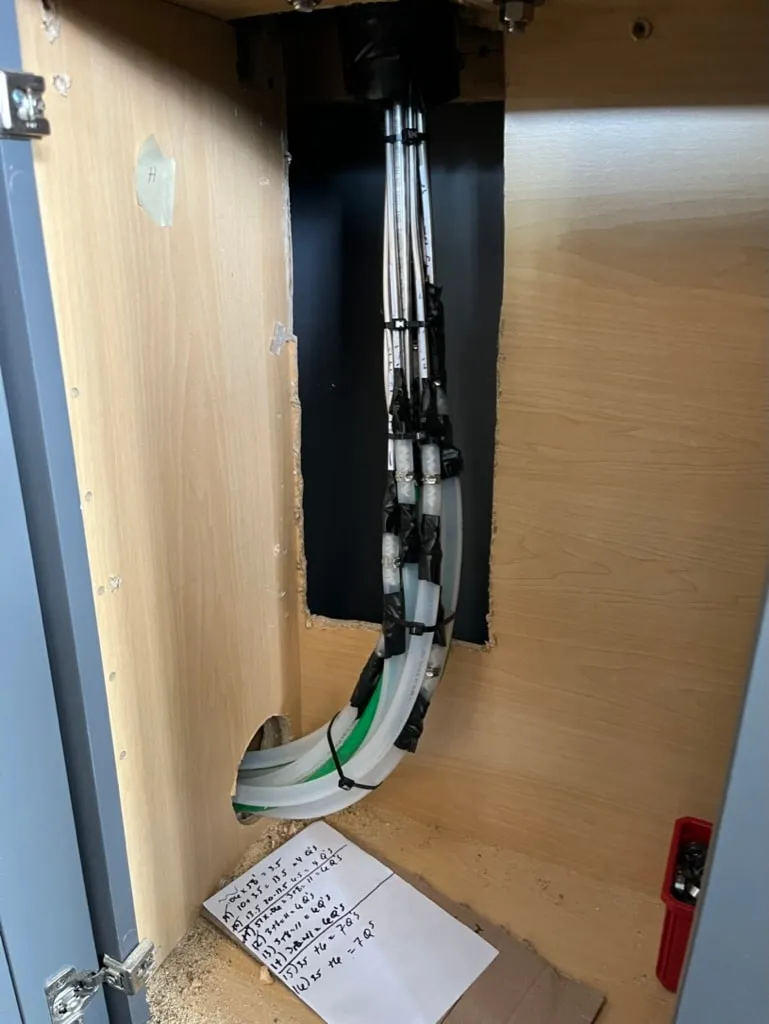
- Vinyl Lines: These are commonly used due to their flexibility and cost-effectiveness. Vinyl lines have a moderate resistance level, making them suitable for shorter runs.
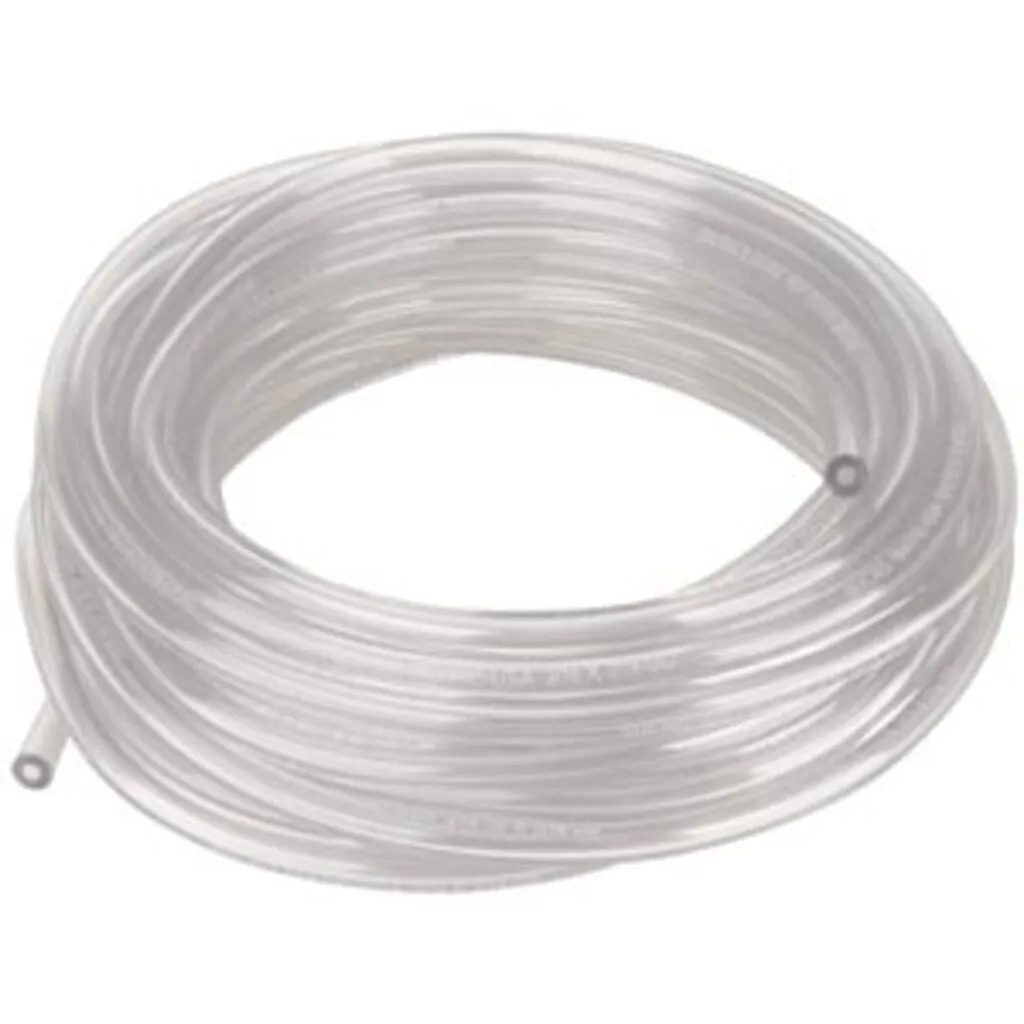
- Barrier Tubing: This type involves multiple layers, typically including a gas barrier which helps maintain the beer's flavor and carbonation. Barrier tubing usually has similar resistance levels to vinyl lines.
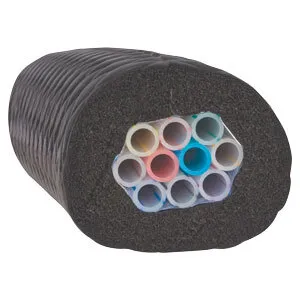
It's important to recognize that line resistance directly impacts the balance of a draft system. Beers require a specific applied pressure to dispense correctly, which must counteract the line's inherent resistance to maintain the product at the desired carbonation and flow rate.
For further guidance on understanding line material specifics and how they relate to maintaining a clean and balanced draft system, one might consider referring to Renny's Post on Beer Lines. Here, one will find more detailed information on beer lines, their properties, and how they fit into the broader draft beer system.
The concept of line resistance is not just theoretical; it has practical implications for serving quality beer. Using the right combination of pressure, temperature, and tubing can result in a perfectly poured pint, and knowing the resistance value of the chosen material is a cornerstone of this process.
Optimal Configuration for Draft Beer Systems
Adjusting a Self-Contained Draft System
When calibrating a self-contained (direct draw) draft system, one must take into account several key factors:
- CO2 Pressure: The amount of pressure from the CO2 regulator setting needs to be precise to maintain the beer's carbonation level. Usually 12-14 PSI of Co2.
- Elevation Change: Measure the vertical distance from the keg's middle to the faucet. Even a small change can impact the necessary pressure.
- Beer Line Resistance: Each line has an intrinsic resistance that affects the flow rate, typically measured in pounds of resistance per foot of line.
- Temperature: Dispensing draft beer at 38 degress.
Adjusting a Long-Distance Beer System
For more intricate long-distance or remote beer systems, which commonly use a glycol cooling system to maintain temperature:
- Temperature Maintenance: The beer must be kept at a constant temperature from keg to faucet to prevent over-foaming and under-carbonation.
- Pressure and Carbonation Equilibrium: Gauging the right pressure to apply for the CO2 is crucial to retain the beer’s fizziness without causing excess foam. Possibly blended gas for longer runs or use of beer pumps.
- Advanced Calculations for Line Resistance: Due to the longer lines and potential for greater temperature variance, more sophisticated calculations might be required to adjust for the increased complexity. Selecting the right trunk line for long-draw beer systems is essential as it affects static and dynamic resistance, ensuring proper flow rates and overall system efficiency.
The goal remains to keep the system balanced to ensure optimal dispensing conditions for the beer.
The Critical Role of Proper System Calibration
A system that is well-balanced provides consistent quality and taste which are paramount for beer enthusiasts. A balanced system also eliminates common issues like:
- Excessive Foam: Caused by too much pressure or inadequate line resistance.
- Flat Beer: Caused by too little pressure which doesn't maintain carbonation.
- Maximized Keg Yield: Getting the highest ROI from your draft beer system
Moreover, efficient beer delivery saves costs by reducing waste and increasing customer satisfaction and convenience. The precise adjustment of pressure and temperature, alongside the correct line length, leads to the perfect pour each time.
Achieving Optimal Balance in Draft Beer Systems
Balancing a draft beer system requires precise control over the flow of beer from the keg to the faucet to ensure that it pours smoothly and with the correct level of carbonation. Here are key considerations for calibrating your system:
- Appropriate Pressure: Carbonation in the keg is maintained by CO2 pressure. Set the regulator to match the beer type and desired level of carbonation.
- Line Length and Diameter: The length and internal diameter of the beer line affect resistance and need to be matched to the system's pressure. Generally, longer lines increase resistance and help slow the flow for a controlled pour.
- Elevation Changes: Be aware of the rise or drop from the keg to the tap, as gravity will impact the beer's flow rate.
- Temperature Consistency: Keep the beer at the correct, steady temperature to maintain carbonation levels and prevent foaming.
- Component Resistance: Each part of the system, like taps and couplers, adds its own resistance. Factor these into your calculations.
Using this calculation will help avoid issues such as excessive foam and will contribute to the proper dispensing of beer from your system. Guidance from experts can provide added insights into this technical process. Additionally, resources from brands such as Micromatic offer useful tips on managing pressure appropriately for different types of beer.
By methodologically adjusting each element and understanding the respective impact each has, a balanced draft beer system can be achieved for the perfect pour every time.
Maintaining Beer Lines for Optimal Performance
Maintaining beer lines is crucial for optimal performance and to prevent contamination. Regular cleaning and timely replacement of beer lines ensure that the beer is dispensed at the correct temperature, pressure, and flow rate, resulting in a better drinking experience.
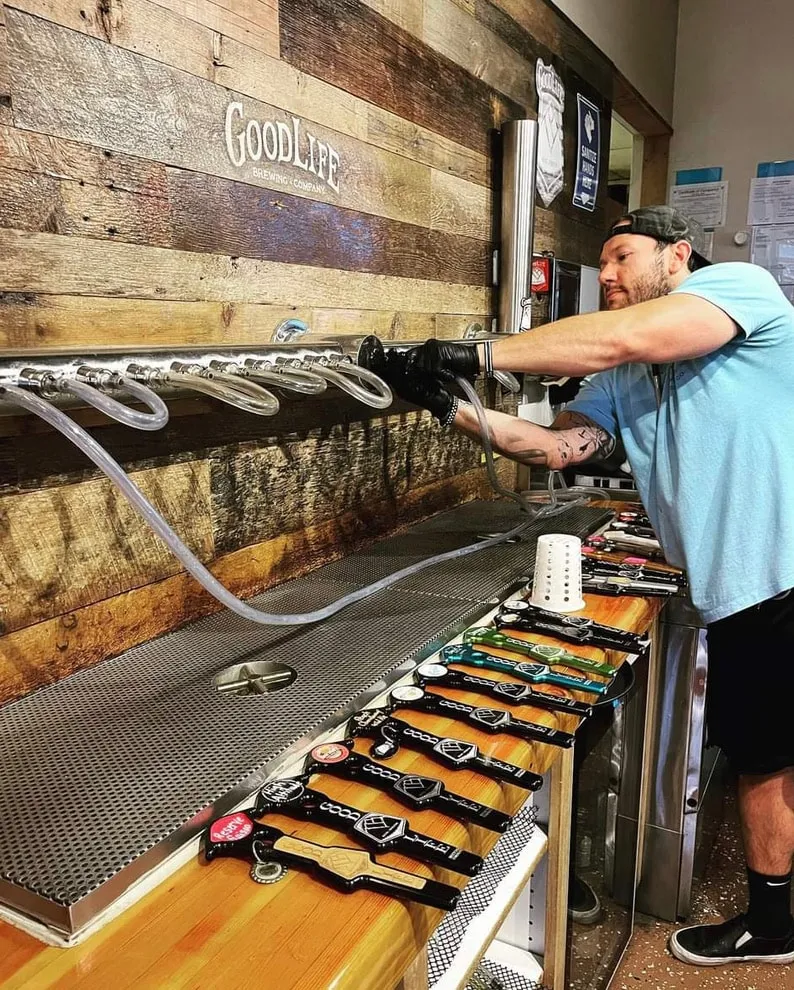
Beer lines should be cleaned regularly with a caustic cleaning solution followed by an acid solution. The frequency of cleaning depends on the usage of the system, but it is generally recommended to clean the lines every two weeks. This routine helps remove any buildup of yeast, mold, and other contaminants that can affect the taste and quality of the beer.
In addition to regular cleaning, beer lines should be replaced every two years or as recommended by the manufacturer. Over time, beer lines can degrade, leading to off-flavors and reduced performance. By adhering to a proper maintenance schedule, you can ensure that your draft beer system continues to deliver high-quality beer.
Proper maintenance of beer lines is essential for any draft beer system, whether it’s a home draft system or a commercial setup. By keeping your beer lines clean and in good condition, you can enjoy a consistently great beer experience.
Common Questions Regarding Beer Line Restriction
Influencing Elements of Beer Tube Resistance
Factors that alter the resistance within beer tubing include the hose length, diameter, and the material it's made from. Every foot of the beer line adds a natural resistance due to friction that the beer faces as it travels through parts of the line, which is often referred to as "line resistance."
Calculating Optimal Beer Line Length for Adequate Flow Control
To establish the appropriate length of a beer line to ensure efficient flow and proper restriction, one needs to consider the balancing equation. This calculation takes into account the resistance per foot of tubing, the total pressure being applied by airlines and the gas system, and the vertical distance between the keg and the faucet.
Diameter of Hose and Its Effect on Beer Line Resistance
The internal diameter of the beer line directly affects the flow resistance. A smaller diameter increases resistance and too much can lead to over-foaming, whereas a larger diameter decreases resistance, potentially causing the beer to pour too quickly if not accounted for in pressure settings.
Role of CO2 Pressure In Setting Restriction in Beer Lines
The CO2 pressure settings are essential for controlling the speed of the beer flow. Higher pressure can compensate for long lines or those with a wider diameter, ensuring beer is dispensed at a controlled pace without excess foam.
Traits of an Equilibrium in Draft Beer Systems
A well-balanced draft beer system delivers beer with the intended level of carbonation, at the correct temperature, and with the proper rate of flow. It minimizes foam and maintains the quality of the beer from keg to glass. Pours at a steady 2 ounces per second.
Material of Beer Lines and Its Internal Resistance Implications
The material from which a beer line is made can influence its resistance. Common materials include vinyl, stainless steel, and polyethylene, with different properties affecting the smoothness of the interior surface and thus the level of resistance encountered by the beer as it flows through the line.
Troubleshooting Common Issues
Common issues with draft beer systems include excessive foam, inconsistent flow rate, and beer quality problems. These issues can be caused by a variety of factors, including incorrect keg pressure, improper beer line length, and poor system maintenance.
Excessive foam is often a result of too much pressure or inadequate line resistance. To troubleshoot this issue, check the keg pressure and ensure it is set correctly for the type of beer being dispensed. Additionally, verify that the beer line length and diameter are appropriate for the system’s pressure settings.
Blockages or kinks in the beer line can cause inconsistent flow rates. Inspect the beer lines for obstructions and ensure they are properly installed without sharp bends. Regular maintenance and cleaning can help prevent these issues from occurring.
Beer quality issues, such as off-flavors or flat beer, can result from poor system maintenance or incorrect temperature settings. Ensure that the beer lines are cleaned regularly and that the system is calibrated to maintain the correct temperature and pressure.
By understanding the components of your draft beer system and how they interact, you can effectively troubleshoot and resolve common issues. This knowledge will help you maintain a well-balanced system that delivers high-quality beer every time.
Overview of Beer Line Restriction
Understanding beer line restriction is crucial when setting up a draft beer system. This resistance slows the beer flow to ensure the right pace and carbonation. Key points include:
- Resistance Value: Measured in pounds per foot; thinner lines provide more resistance.
- Line Diameter: Common sizes are 3/16", 1/4", and 3/8", with 3/16" ID typically offering 3 lbs/ft resistance.
- Beer Style: Different styles require varying carbonation and flow rates.
- Temperature and Pressure: Affect CO2 solubility; adjustments in line specs maintain carbonation.
- Materials: Options like vinyl or stainless steel impact taste and cleanliness.
Balancing these factors ensures optimal beer pouring with the right foam and flow. For more details, refer to the Draught Quality Manual. For assistance, contact Renny's. Cheers!