The Beer Pump: Ultimate Beginners Guide And Tutorial
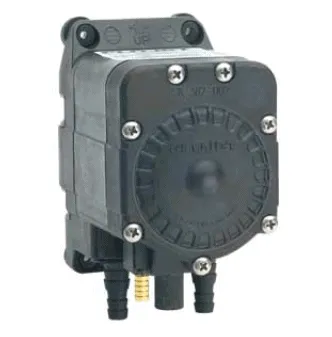
In this post I’m going to talk about using a beer pump and how to dispense draft beer on commercial systems with one. I’ll cover all the main points how to use it, how to operate it, how to maintain it and clean it.
After this post you’ll see why beer pumps play such a pivotal role in dispensing draft beer over long distances. Also, the advantages of using them over blended gas.
Here we go!!
What is a Flojet Beer Pump?
A beer pump is a device we use to pump draft beer long distances from a beer cooler without compromising the integrity of draft beer. Pumps are also used with brite tanks, and casks to dispense beer when added pressure is needed.
Typically, there are a few ways to push beer in a draft system. Either mixed gas, or Co2. Using Co2 we can activate beer pumps. I've heard you can use Nitrogen with them, but I I’ve never done that. I prefer beer pumps on longer remote systems over 200+ feet, and using blended gases on smaller runs.
So here's a picture of a Flojet Beer Pump Below:
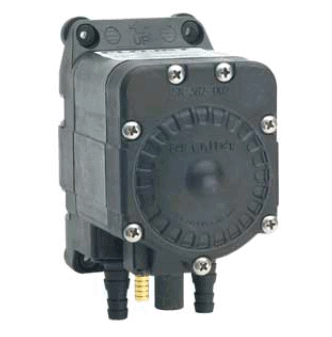
Flojet Beer Pump
Now beer lengths, or beer runs less than 40 feet can use pure C02 on their systems pushing beer. But I would default to a mixed gas of 70 percent C02-30 Percent Nitrogen. On all runs under 40 feet. Simply because we can get great pour with a blended gas, and add pressure without over carbonating a beer.
In the event of a long beer run. Either a beer pump or mixed gas needs to be used.
Mixed gas can be used 70 percent C02 and 30 percent Nitro would work. These pre-mixed cylinders are sourced from your local gas distributor. Gas blenders could also be another option, instead of pre-mixed cylinders.
Overall, the beer pump helps pour beer long distances on remote systems up to 800’ without having to use mixed gas. If your beer needs to travel up multiple floors. This is where beer pumps excel.
How Does a Beer Pump Work?
The pump setup requires two operational regulator pressures. CO2 pressure on the keg to maintain beer carbonation ( 12-14 psi), and separate gas pressure to the beer pump ( 20+) to propel the beer to the faucet.
The pump receives pressure from either C02 or dry compressed air. Regulated by a secondary regulator. The operating pressure of the pump is 10 psi up to 90 psi. The pump has 2 ports, a receiving port. Which connects to the beer coupler. The other outlet supplies the beer system with beer and that fitting is usually connected to a FOB, and then to the beer trunk line.
F.O.B
FOBs stop the flow of beer through a line once the keg empties. This reduces the beer loss associated with changing a keg and reduces operating costs.
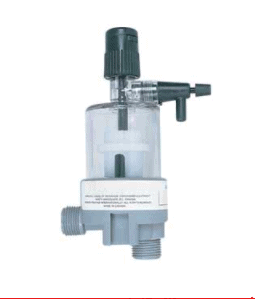
Beer FOB used to keep beer lines full after a keg blows.
Available in different designs, most feature a float in a sealed bowl that drops when beer flow from the keg stops. The FOB allows the beer lines to stay packed. This makes for less product loss and generates savings for the account.
Venting The Pumps
Now if C02 powers the beer pump there’s a hose fitting on the front side of the beer pump. It’s a ¼” I.D. this is the pump vent and it needs to be vented outside of the the beer cooler.
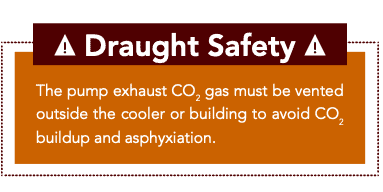
When the pump operates, in exhales C02. The pumps needs to vent outside the beer cooler. If compressed air powers the pump, no need to vent the pumps.
What Gas is Used to Pump Beer?
2 types of gas are used to fire up the beer pump. It's c02 and compressed air. Like I mentioned earlier I've heard of Nitrogen, but haven't used it personally.
I’ll use c02 70 percent of the time because the properties I’m working on usually house bulk C02 on property. Here's a post for the right C02 cylinder sizes if you are using cylinders.
Compressed air is also an option. Just make sure you use oil-less compressors with the beer pumps, and make sure the compressors are vented from time to time. They accumulate moisture in their tanks and if they aren't vented. The pumps will be compromised due to moisture.
How to Clean a Pump?
You clean the beer pump the same way you would clean beer systems. You will also need a Flojet Reversal valve to clean the beer pump properly. With the Flojet reversal valve inserted into the pump you can recirculate chemicals the proper way.
- First, step would be to flush out all the beer in that line with water. Then add your cleaning solutions. Caustic cleaning solution every 2 weeks and Acid cleaning solution every 4 weeks.
Since the pump would likely be part of a remote beer system. A re-circulating pump would work. Cleaning the beer system and beer pump. Circulating cleaning solution for at least 15-20 minutes.
- Next, rinse the solution out of the lines until the ph paper tests between 7-8. This will tell you that the lines are ready to tap beer, and free of cleaning solution.
The reversal valve hooks into the bottom of the pump. It helps with beer cleaning by changing the the flow while the system re-circulates. The re-circulation method is by far the best cleaning method to date for beer systems.
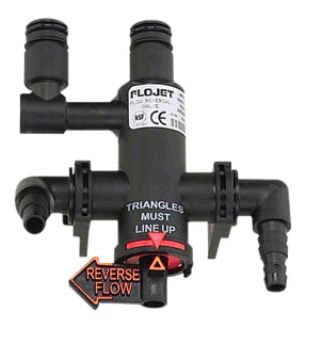
This Reversal Valve helps change flow direction, and helps clean lines.
Flojet Beer Pump Troubleshooting
The beer pumps are pretty straight forward after you hook it up. The pump will regulate itself automatically. However, there are times when the pump fails or isn’t working correctly.
If gas is powering the pump and the keg runs out of beer. The pump continues to pump without beer in it you can damage diaphragm itself. This only happens if the beer pump isn’t connected to a FOB inside the cooler room.
A direct connection to a beer trunkline and an empty keg will continue the pump to operate until its broken.
IF the ⅜ hose fittings crack for whatever reason they can be replaced.
Sometimes the O-rings need to be replaced because they can be cracked.
Brass fittings, where the gas enters the pump will need to be replaced sometimes because they get damaged.
Outside that they’re very reliable and should you encounter some problems what I mentioned above are usually the culprits. For foamy beer issues I recommend checking that link out.
Summary
In closing the beer pump is a great tool to use when dispensing beer over long distances. It’s better than using mixed gas because there’s no nitrogen in contact with beer.
Using a beer pump also allows you to dial in the right pressure to get the right flow needed, maximizing keg yield.
The pump can also be used on casks and brite tanks.
Maintenance is minimal and once the pump is set up and primed you shouldn’t have to worry about it.
Buy Beer Dispensing Equipment:
- Beer Pump
- Beer FOB
- Flojet Reversal Valve ( For Cleaning Beer Systems With Beer Pumps )
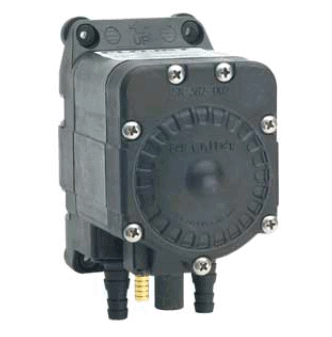
Flojet Beer Pump
If something needs replacement, check the hose fittings, gaskets and brass fittings. If using C02 to power the pump make sure to vent the pumps outside the beer cooler.
If you’d like to order a beer pump click the link, and if you would like some more information about draft beer dispensing please check out our blog.
Cheers!