The Beer Nitrogen Generator: Elevating Your Draft Beer Dispensing
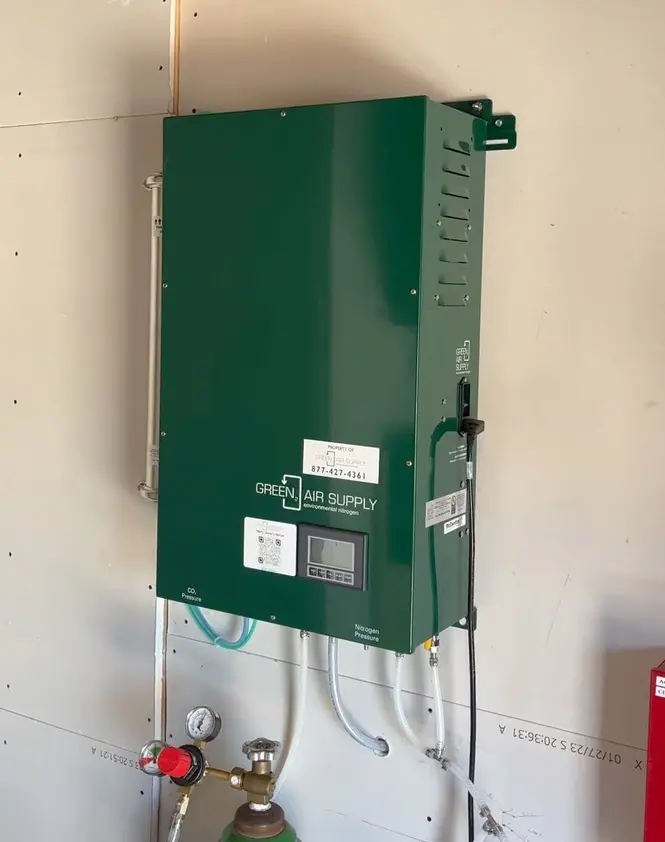
Nitrogen generators have revolutionized the whole beverage dispensing industry, notably in beer dispensing, where their usage has become increasingly popular.
These systems allow for the on-site production of nitrogen gas, which is essential for pouring the perfect pint when using a blended gas.
Instead of relying on external CO2 sources, breweries and pubs can now generate their own, endless supply of nitrogen, resulting in a fresher and more cost-effective pour.
The technology not only streamlines operations but also offers control over the quality of beer served, ensuring that it meets the brewer's intended flavor profile and carbonation level.
The incorporation of nitrogen generators in the beer industry aligns seamlessly with the growing emphasis on sustainability.
By producing nitrogen in-house, businesses are able to reduce their environmental footprint, cutting down on the transportation and handling of high-pressure cylinders.
Maintenance of these nitrogen generators is generally minimal, ensuring that the technology remains an asset rather than a liability in the day-to-day operations of a brewery or bar.
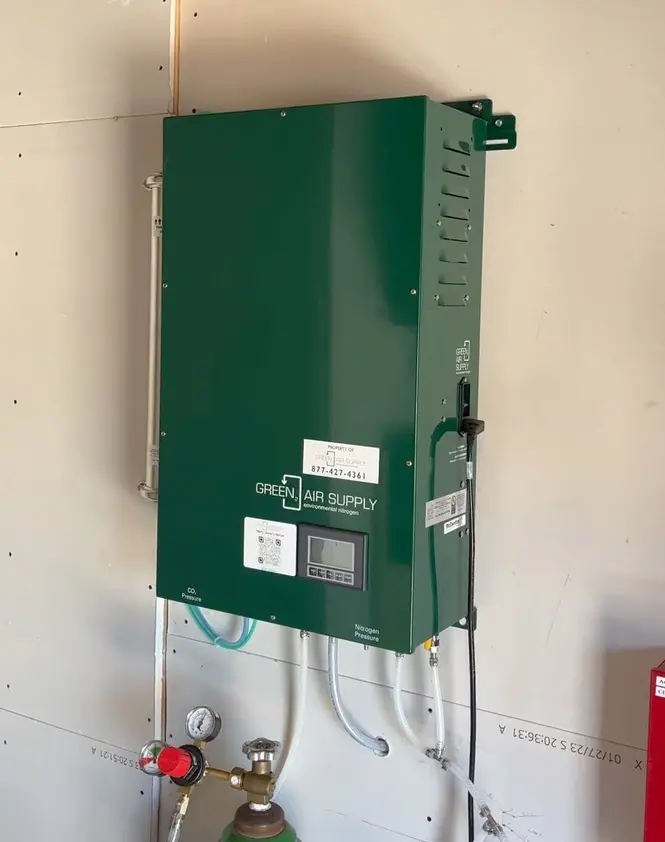
Key Takeaways
- Nitrogen generators are pivotal in improving the quality and carbonation consistency of beer.
- The technology enhances sustainability and reduces operational costs for businesses.
- Minimal maintenance is required, making nitrogen generators a reliable asset in beer dispensing.
Understanding Nitrogen Generators
Nitrogen generators are crucial equipment for industries requiring nitrogen gas, providing a steady, cost-effective supply. They eliminate the need for nitrogen cylinder deliveries, offering convenience and operational efficiency.
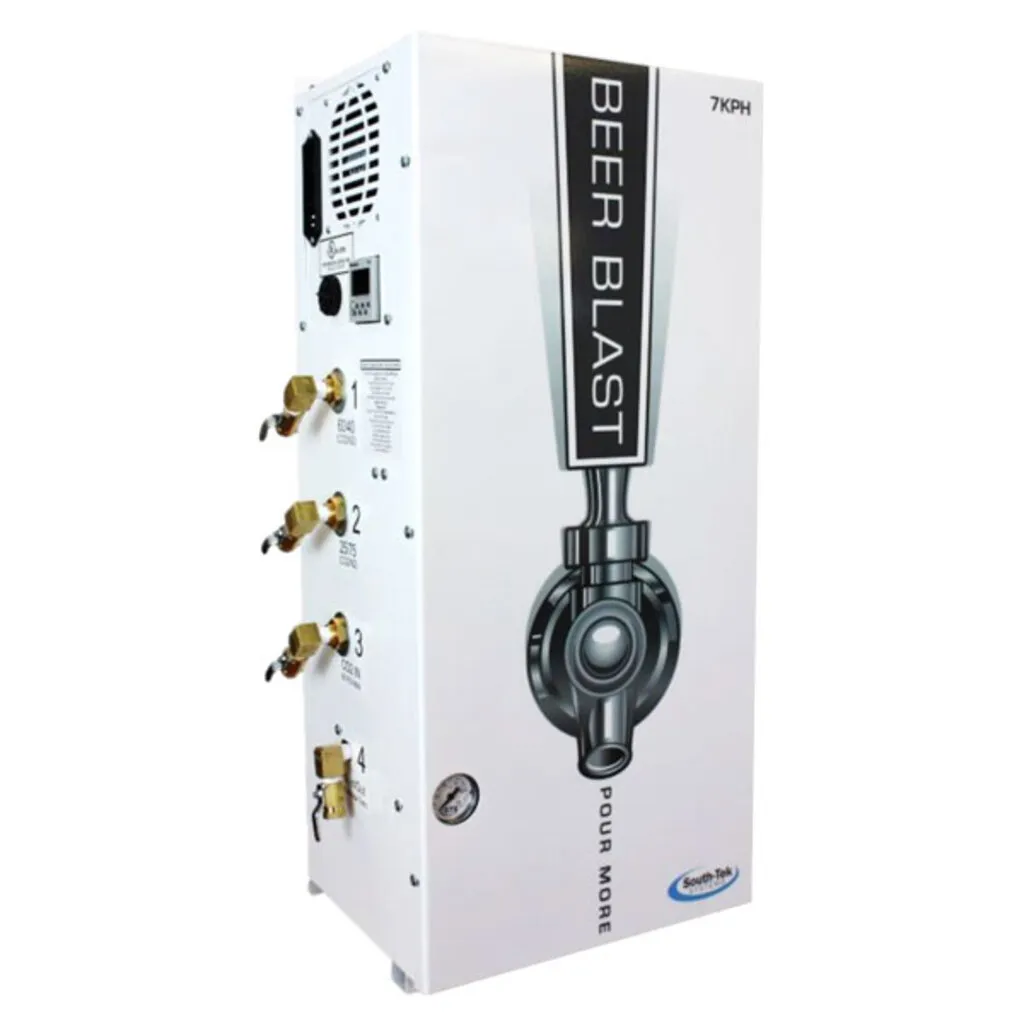
Principles of High-Purity Nitrogen Gas Generation
Nitrogen generation technology is rooted in separating nitrogen from other atmospheric gases. An essential component in this process of dispensing draft beer. Nitrogen is typically stored in a storage tank next to the separator or generator. These units usually have a specified blend and a Guinness gas blend. More custom blends can also be added to the unit. Ultimately, the purity of the nitrogen doesn't compromise the integrity of the draft beer. Therefore helping the beer taste as the brewer intended.
Two primary methods exist: Membrane nitrogen generators and Pressure Swing Adsorption (PSA).
The membrane technique filters out oxygen, water vapor, and other impurities, producing nitrogen blends suitable for various applications.
Conversely, PSA operates by adsorbing unwanted gases onto a material surface, releasing pure nitrogen at high purities.
Types of Nitrogen Generators
Various nitrogen generators are tailored to specific needs and applications, including the cost-effective use of a nitrogen generator system for dispensing draft beer and wine on tap. These systems offer lower operating costs and higher purity of nitrogen gas, which is essential for maintaining the quality and freshness of the beverage.
Onsite nitrogen generators, like membrane and PSA systems, provide a continuous nitrogen supply by processing compressed air. This capability allows businesses to bypass gas distributors, reducing overall costs and minimizing downtime for their draft beverage systems.
Membrane models are recognized for consistency in nitrogen purity, while PSA systems are lauded for delivering pure nitrogen for more sensitive uses.
Green Air Supply Nitrogen Separator
Among the types of nitrogen generators, a green air supply nitrogen separator is an eco-friendly option.
It produces nitrogen gas without releasing pollutants into the atmosphere. This system is integral for businesses striving to reduce their carbon footprint while maintaining efficient operations.
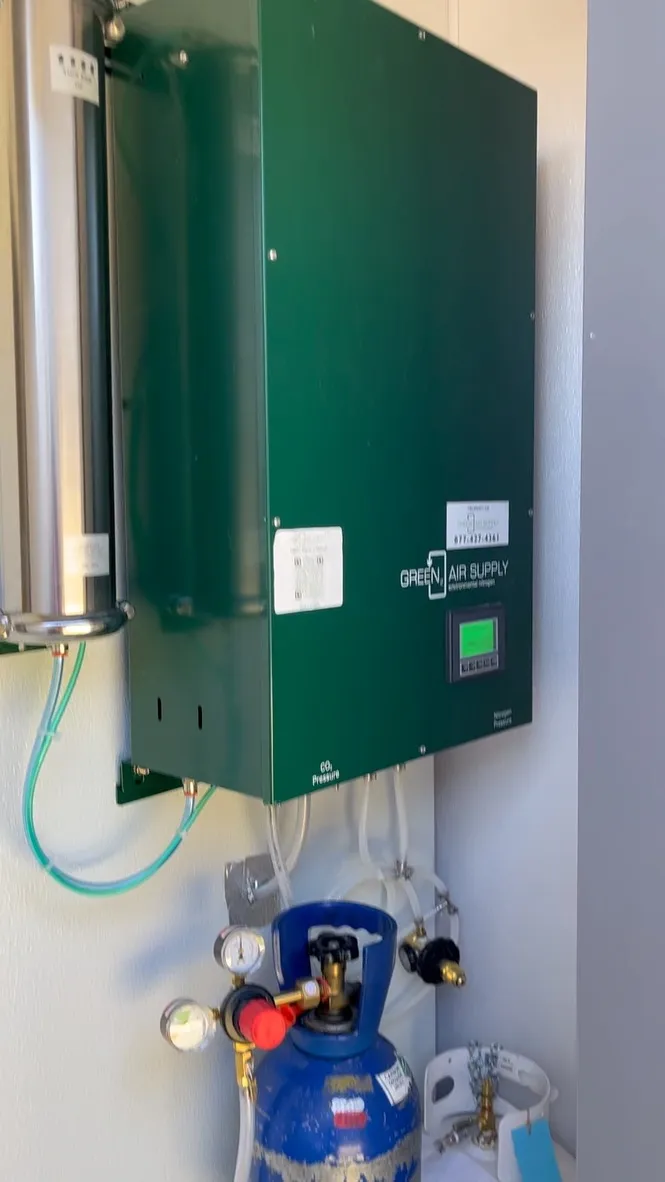
Advantages of a Nitrogen Generator
Businesses invest in nitrogen generators for their numerous benefits:
- Cost Reductions: They can significantly lower expenses compared to purchasing bottled nitrogen. Additionally, a nitrogen gas generator offers ease of use and cost savings, presenting a more reliable and efficient alternative to traditional nitrogen supply methods.
- Supply Reliability: An onsite nitrogen generator ensures an uninterrupted nitrogen supply, eliminating potential delays caused by cylinder delivery issues.
- Purity Customization: Operators can adjust the output for specific nitrogen purity levels, allowing for tailored applications from food packaging to electronics manufacturing.
Implementation and Maintenance
Implementing a nitrogen generator into a brewery’s operations can significantly enhance both the quality of beer and the efficiency of the dispensing process. Incorporating a secondary regulators supply is essential for maintaining the optimal blend of nitrogen and CO2, which is crucial for dispensing beverages from draft system kegs with precision. This setup not only ensures operational efficiency but also emphasizes the importance of reliability and monitoring to troubleshoot potential issues and ensure a consistent supply. This section will delve into the specifics of the installation process, including the integration of a secondary regulators supply, and the ongoing costs and considerations for maintenance, which are crucial for achieving a favorable return on investment (ROI) and minimizing downtime.
Installation Process
The installation of a nitrogen generator requires careful planning and a few key steps.
Initially, one must ensure that the space used for installation meets the necessary requirements, such as proper ventilation and power supply.
According to Renny’s Draft Solutions, installation involves setting up an onsite gas blender and nitrogen extraction unit. For those requiring precise control over their gas blends, the option to include an external gas blender with the nitrogen generator installation is available.
Most systems come with comprehensive guides helping to ensure the setup process is as smooth as possible.
Operating Costs and Maintenance
Once installed, nitrogen generators are relatively low in terms of operating costs and maintenance.
Regular service calls should be scheduled to ensure the system runs optimally, but these are generally minimal compared to the costs associated with CO2 cylinders.
Generators are designed to be eco-friendly, reducing the carbon footprint associated with gas delivery.
Nonetheless, maintenance is crucial; as stated by Micromatic, it ensures a consistent supply of the correct blend of CO2 and nitrogen, essential for the perfect pour.
Maintenance tasks typically involve periodic filter replacements and system checks to prevent downtime and maintain the quality of beer dispensed.
Applications in Dispensing Draft Beer
Nitrogen, an inert gas, plays a pivotal role in beer dispensing, particularly in developing nitrogenated beer styles that offer a distinct texture and quality to draught beer. This inert gas is crucial for achieving a different flavor profile with lower CO2 content, preventing foamy beer, and ensuring the draft beer itself remains fresh for longer by slowing down oxidation and preventing contamination. By understanding the interplay between nitrogen and CO2, as well as the benefits and equipment used, breweries can enhance their draft beer offerings. The use of nitrogen generators over traditional nitrogen cylinders for providing beverage gas on demand presents significant advantages, including cost savings, convenience, and reliability. This ensures that breweries can avoid downtime and lost sales, making nitrogen generators an essential tool for dispensing perfectly carbonated and well-presented draught beer, as well as other nitrogenated drinks like cold-brew coffee, tea, craft cocktails, and juice.
Nitrogen vs. CO2 in Beer
Nitrogen gas and carbon dioxide (CO2) are both used in beer carbonation, but they impact the beer's properties differently.
CO2 is more soluble in beer and creates the sharp, tingling sensation associated with carbonation. Nitrogen, less soluble than CO2, results in a smoother, creamier beer texture, having minimal effect on beer's flavor.
This makes nitrogen ideal for certain styles like stouts and porters.
For example, nitrogenated beers like Guinness require a blend of 75% nitrogen and 25% CO2 to achieve the optimal taste and mouthfeel.
Enhancing Beer Quality with Nitrogen
Using nitrogen in beer dispensing can significantly enhance beer quality.
Nitrogen-infused beers, often referred to as nitro beers, are known for their smoother and creamier texture compared to their carbonated counterparts.
Besides stouts and porters, nitrogen can also be used in ales and lagers to give them a softer finish while maintaining the desired carbonation level - typically with a gas mix of 70% nitrogen and 30% CO2.
Equipment for Nitrogen Beer Systems
An integral part of nitrogen beer dispensing is the equipment used, such as nitrogen cylinders or a beerblast® nitrogen generator, which produces nitrogen from atmospheric air. Purchasing nitrogen gas cylinders from a gas distributor, however, comes with disadvantages such as higher expenses, space occupation, and the potential inconvenience of waiting for deliveries, making an onsite beer nitrogen generator perhaps a more efficient option.
This system feeds beverage gas into a mixed gas beer dispensing system, allowing for consistent and quality draft beer.
Nitrogen generators can supply an onboard nitrogen gas generator and blender, ensuring the correct nitrogen and CO2 blend for different types of beer.
Properly implemented equipment maintains draft beer quality and can accommodate the needs of craft beer establishments seeking to have draft beer systems provide a superior drinking experience.
Business Benefits and Environmental Impact
Incorporating a full nitrogen generator system can be a strategic move for craft breweries, leading to both financial advantages and environmental gains. The adoption of this technology translates into direct cost savings and efficiency enhancements while also promoting sustainability and reducing the carbon footprint of brewing operations.
Cost Savings and Efficiency
Nitrogen generators enable breweries to produce their own nitrogen gas on-demand, reducing the dependency on high-priced, delivered cylinders.
Not only does this draft system result in cost savings from decreased delivery fees, but it also streamlines production processes.
Breweries can often see a return on investment within a few years, as the convenience of on-site generation allows for continuous operations and eliminates downtime related to cylinder changeovers.
The importance of the purity and reliability of the nitrogen produced by onsite nitrogen gas generators, cannot be overstated, especially when it comes to dispensing beverages. This ensures that the nitrogen gas is of the highest quality for beer enthusiasts enjoying nitrogenated beers.
A study points out that the consistent supply of nitrogen gas boosts efficiency, particularly when dispensing nitrogenated beers, which are growing in popularity among beer enthusiasts.
Sustainability and Eco-Friendliness
Utilizing an on-site nitrogen generator is a step towards a more sustainable and eco-friendly business model.
These systems contribute to a lower carbon footprint by reducing the transportation requirements and the associated emissions from gas deliveries.
Craft breweries are now able to produce custom nitrogen blends full of gases needed for optimal beer dispensation while adhering to eco-conscious practices.
Additionally, nitrogen is a more sustainable gas choice, as it helps keep beer fresher for longer periods, reducing waste.
As environmental awareness and regulations become increasingly stringent, adopting nitrogen generation methods aligns craft breweries with green best practices.
Summary
Nitrogen generators are an increasingly popular choice for beer systems. They can produce on-demand nitrogen gas for optimal beer dispensing.
They are particularly crucial for nitrogenated beers. These beers rely on a specific blend of nitrogen and CO2 to achieve the right taste and mouthfeel.
Installing a nitrogen generator offers a variety of benefits. These many benefits include operational efficiency, cost savings, and consistent quality.
The typical mixture for dispensing stout beers like Guinness is composed of 75% nitrogen and 25% CO2. The introduction of a nitrogen generator enables a brewery to create this balance in-house.
It also decreases the reliance on external CO2 sources and reduces the impact of CO2 shortages. In addition to improving the quality of the beer, nitrogen generators also contribute to maintaining proper pressure in the dispensing system, which is paramount for the perfect pour.
Cost-effectiveness is another significant advantage. While the initial investment may be substantial, nitrogen generators can lead to substantial operational savings ranging from 40% to 90% compared to traditional gas delivery methods.
They can also be cost-effective in the long term, with some systems paying for themselves in under two years.
For craft breweries, nitrogen generators are not only vital for the dispensing draft beer, but also for processing, such as tank transfers where an inert atmosphere is essential. They can provide high-purity nitrogen gas, up to 99.5%, which is crucial for various brewery operations.
Nitrogen generators have a small footprint and the potential for wall mounting. This makes it easy to integrate them into existing brewery setups. They ensure that breweries can produce nitrogen gas as needed, without excess waste or storage challenges.