Insulated Beer Line: Maximizing Draft Quality and Efficiency
.webp)
Insulated beer lines are essential for maintaining the quality of draft beer from keg to glass. These lines keep the beer cold and fresh by circulating cold glycol around the beer lines. To achieve this, insulated lines use glycol cooling systems that prevent temperature fluctuations and spoilage.
An insulated beer line typically consists of a cluster of beer lines surrounded by glycol lines, all enclosed in foam insulation. This setup helps prevent heat gains and keeps the beer at a consistent temperature, which is crucial for the perfect pour. Whether you are running a bar or setting up a home kegerator, understanding the role of insulated beer lines can vastly improve the taste and longevity of your beer.
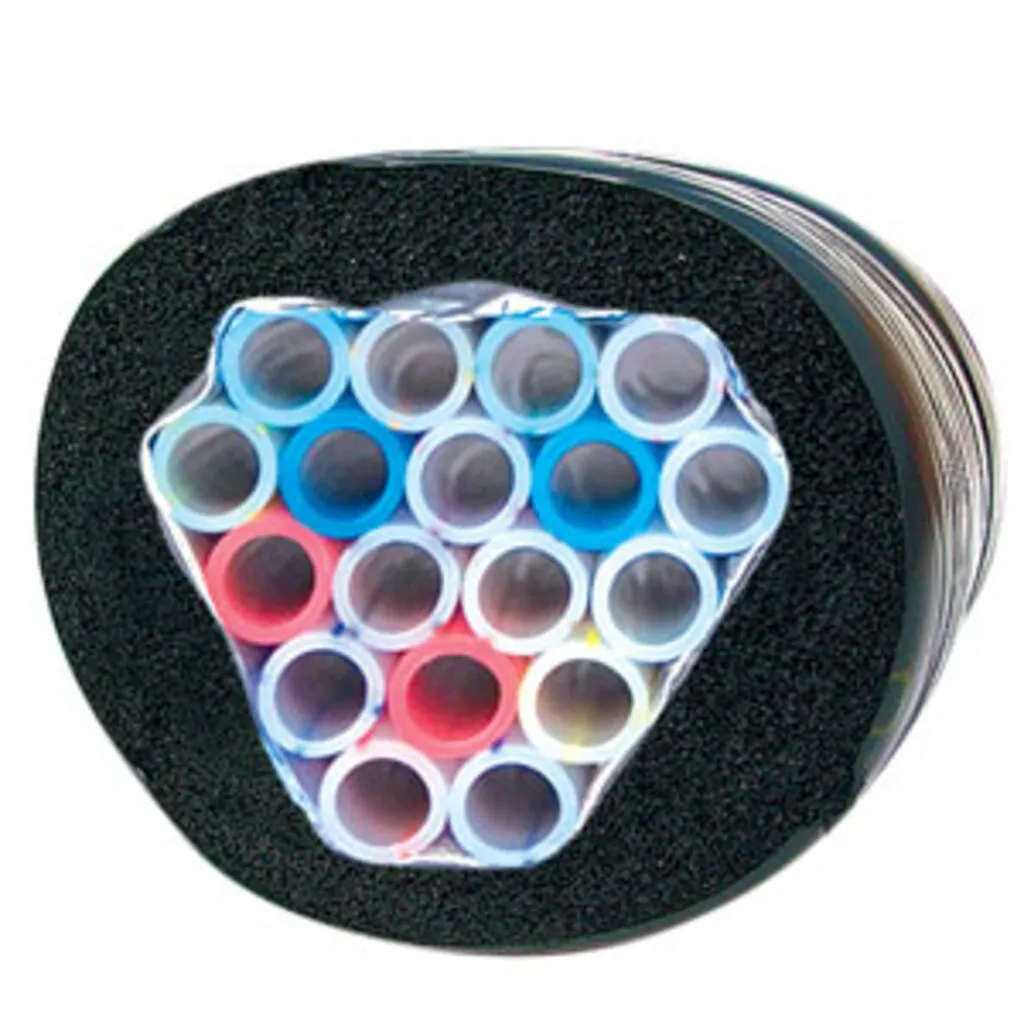
Proper installation and regular maintenance of insulated beer lines are key to enhancing the overall draft beer experience. Neglecting these aspects can lead to poor beer quality and increased costs due to spoilage. Dive into the details to ensure you’re serving the best beer possible.
Key Takeaways
- Insulated beer lines keep beer cold and fresh.
- They use glycol cooling systems to prevent temperature fluctuations.
- Proper installation and maintenance enhance the draft beer experience.
Understanding Insulated Beer Lines
Insulated beer lines are essential components in any draft beer system, ensuring temperature stability and quality. They help prevent temperature fluctuations and condensation, thereby maintaining the beer’s taste from the keg to the tap. The dispensing point is crucial in this process, as it ensures the beer remains at optimal temperatures from storage to the tap.
Types of Insulated Beer Lines
Beer lines come in various types, each designed for specific needs. Common types include glycol lines and plain insulated beer lines. Glycol lines run alongside beer lines within an insulated bundle known as a trunk line and are often used for longer runs to ensure consistent cooling.
Plain insulated beer lines generally use materials like foam insulation and virgin PE tubing for short distances, providing primary barrier protection against temperature changes. For added durability, some lines feature an extruded jacket or PVC tubing.
Importance of Insulation
Insulation plays a critical role in maintaining draft beer quality. Proper insulation helps prevent temperature fluctuations that can adversely affect beer taste. It also reduces condensation, which can be problematic in areas with varying temperatures.
Without adequate wall insulation, beer lines could experience issues like foaming, which can lead to wasted beer and inconsistent pours. Insulated beer lines help maintain a stable temperature, ensuring a 2 oz per second flow and beer the brewer intended.
Materials Used in Insulation
Several materials are commonly used in the insulation of beer lines. Foam insulation is popular for its effectiveness and ease of application. It’s often paired with aluminized PP film wrap for added thermal protection.
Some systems use Barriermaster Flavourlock™, a specialized material that minimizes flavor contamination. The careful combination of these materials ensures the beer remains at the optimal temperature as it moves from the keg to the tap.
For longer runs, glycol lines wrapped in foil or other reflective materials help maintain temperature efficacy.
Insulated beer lines, constructed from these materials, form the backbone of an efficient and reliable draft beer system.
Components of Draft Beer Dispensing Systems
Draft beer dispensing systems consist of several key components that ensure a smooth, cold, and reliable pour. These include the insulated draft beer tower, lines that connect kegs or barrels in a cooler to the faucets of the draft beer towers and taps, power packs and glycol chillers, and beer line configurations. The draft tower is crucial for maintaining a consistent temperature, ensuring optimal beer quality.
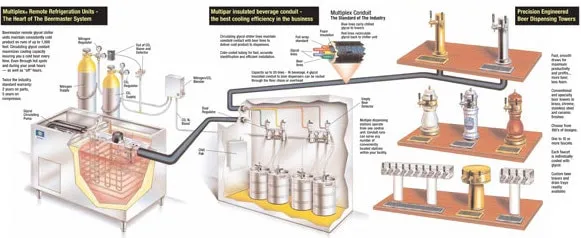
Draft Beer Towers and Taps
Draft tower or beer towers are the visible part of a draft beer system. They hold the beer lines and taps, allowing beer to be poured directly into a glass. Towers come in various materials, such as stainless steel or brass, offering both durability and aesthetic appeal. The taps, or faucets, are attached to the towers and directly control the beer flow.
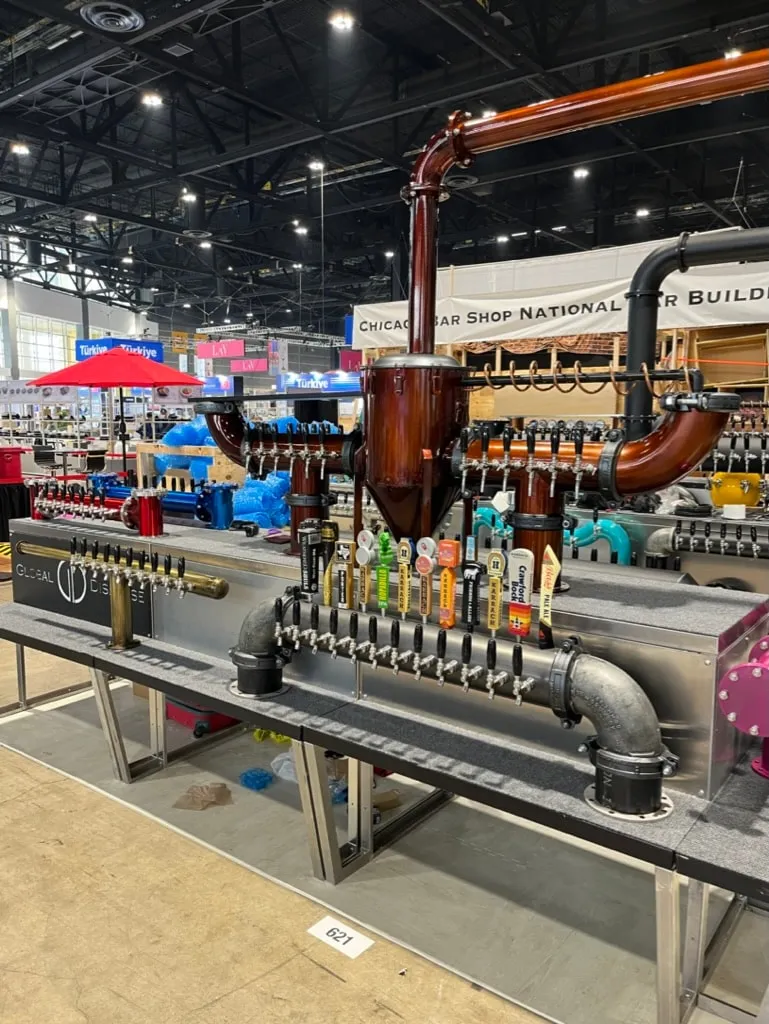
Reliable taps are crucial; designs from companies like Micro Matic are highly regarded. Regular maintenance and cleaning are important to prevent clogs and maintain the quality of the beer. The combination of a well-designed tower and tap ensures each pour is consistent.
Power Packs and Glycol Chillers
Glycol chillers are essential for draft systems that require long beer line runs or are used in commercial settings, as part of specialized glycol systems designed to maintain temperature. Glycol chillers use a mixture of water and glycol to keep beer lines consistently cold. These are usually housed in power packs that contain the necessary machinery to pump and chill the glycol mixture.
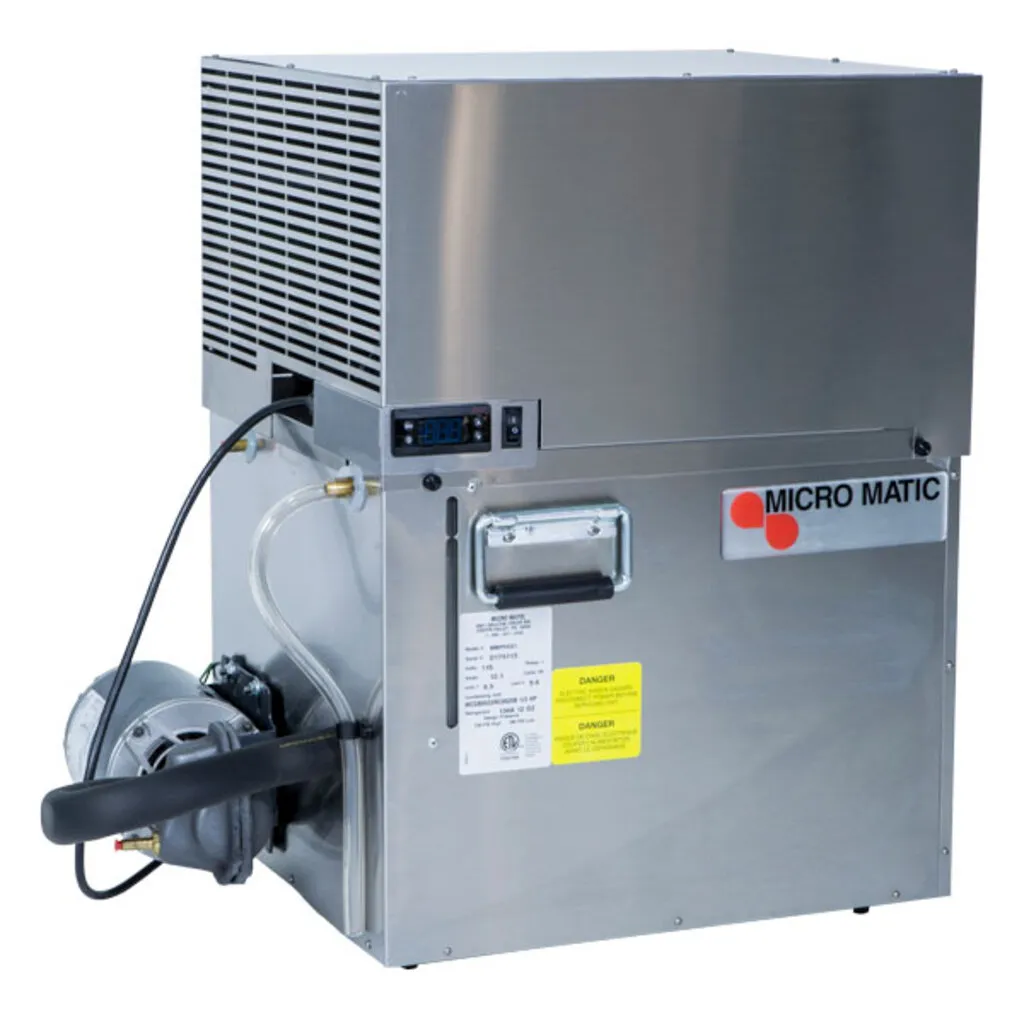
Power packs by companies like U.L. ensure that the beer remains at the ideal serving temperature from keg to tap. This is crucial for preventing bacteria growth and maintaining the beer’s taste. Without a reliable chilling system, the beer can become warm and lose its quality. Additionally, the glycol trunk line, which includes various types of insulated glycol trunk line and lines, plays a vital role in transporting chilled draft beer from coolers to draft towers, maintaining temperature and preventing coolant leakage.
Beer Line Configurations
Beer lines are the conduits that carry beer from the keg to the tap. The configurations can vary based on system needs. A popular option is the beer trunk line, which is insulated and can contain multiple beer lines bundled together. This is ideal for bars with several taps on a single tower.
Another common configuration includes the python system, which often incorporates glycol lines to keep the beer cool over long distances. The choice of beer line impacts the efficiency and reliability of the draft beer system. High-quality lines prevent contamination and ensure that beer flavor remains unaltered.
In summary, a well-maintained draft beer dispensing system relies on the quality and performance of its towers, taps, chilling systems, and beer lines. Regular upkeep and the use of high-quality components ensure a perfect pour every time.
Installation and Maintenance of Insulated Beer Lines
Proper installation and regular maintenance of insulated beer lines are crucial for any commercial setup to ensure optimal performance and profitability. This section covers best practices for installation, maintenance routines, and common issues to troubleshoot.
Best Practices for Installation
Installing insulated beer lines requires attention to detail. Start by selecting high-quality materials like Barriermaster™ Flavourlock Tubing. This helps in maintaining the beer’s taste over long distances. Run the beer and glycol trunk lines together to keep the temperature consistent. These lines should be housed in an insulated beer trunk line.
Insulating the lines with materials like mylar and foam wrap keeps the beer cold as it moves from the kegerator to the tap. Use heavy foam pipe and insulation tape for added efficiency. If running lines under the floor, ensure they are well-sheltered to avoid temperature fluctuations. Additionally, using insulation tape can prevent temperature loss and maintain optimal performance of the cooling systems.
Proper positioning in the cooler or walk-in cooler is essential. Keep lines clear of any obstructive elements that might compromise their integrity. A well-installed system minimizes overhead and improves serviceability by reducing the need for frequent repairs.
Maintenance and Serviceability
Regular maintenance of insulated beer lines is necessary for reliability and efficiency. Perform routine checks for any signs of wear or damage to the insulation. Replace any worn-out segments immediately to prevent CO2 leaks and ensure consistent temperature control.
Clean the beer lines regularly to avoid bacterial buildup. Use appropriate cleaning agents to sanitize both the draft beer trunk line and the glycol lines without damaging the insulation. Detailed attention during these maintenance routines will elongate the lifespan of the system and enhance its performance.
Maintaining serviceability involves periodic checks of the refrigeration unit. Ensure that the glycol power pack is functioning properly and maintaining the temperature required. Serviceability improves profitability by minimizing downtime.
Troubleshooting Common Issues
Even with meticulous installation and maintenance, issues can arise. Temperature inconsistencies are a common problem. Ensure that the insulation is intact and that the glycol power pack is operational. Check the trunk line for any leaks or damages.
Foaming at the tap can indicate CO2 imbalances or microbial contamination. Clean the lines thoroughly and recalibrate the CO2 levels. If the beer tastes off, inspect for potential contamination in the Barriermaster™ Flavourlock Tubing.
Addressing these common issues promptly can save time and costs, ensuring the cold air draft system operates efficiently.
Enhancing Draft Beer Quality and Experience
Using insulated beer lines can significantly improve the quality of draft beer by maintaining a consistent temperature and enhancing the overall experience for customers. This section explores the key factors that contribute to higher quality and a better drinking experience.
Achieving Optimal Temperature Control
Maintaining a beer at a consistent temperature is crucial for preserving its flavor and carbonation. Insulated beer lines, paired with a glycol cooler, help achieve this by keeping the temperature stable from the keg to the tap.
Glycol trunk lines are particularly effective in long-draw draft beer systems, where beer must travel longer distances. These lines are enveloped with glycol coolant, regulated by a glycol pump, ensuring thermal performance throughout the journey. This setup prevents the beer from getting too warm or too cold, maintaining optimal serving conditions. Both the beer line and the coolant lines run through a refrigeration unit, which provides the necessary cooling power.
Summary
Insulated beer lines are essential equipment for maintaining the quality of draft beer. They help keep the beer at a consistent temperature, which is crucial for preserving flavor and carbonation.
Benefits of Insulated Beer Lines:
- Temperature Control: Insulated lines maintain the beer’s temperature from the keg to the tap, ensuring a refreshing pour every time.
- Reduced Foaming: Proper insulation reduces unwanted foaming, which can spoil the beer and waste product.
- Enhanced Flavor: By keeping the beer at its optimal temperature, the original flavors and carbonation are preserved.
A significant advantage is the reduction of temperature fluctuations. Temperature changes can cause the beer to lose its intended taste and texture.
There are various types of insulation materials available. These can include foam, rubber, or even specialized materials like Barriermaster Flavourlock™ tubing. The right choice depends on the specific needs of the draft system and the distance the beer travels.
Key Takeaways:
- Improved Quality: Insulated lines keep beer fresh and flavorful.
- Efficiency: They help reduce waste by minimizing foam.
- Flexibility: Available in different materials to suit various systems.
For anyone serious about serving great-tasting draft beer, investing in insulated beer lines is a smart decision. This not only enhances the customer experience but also ensures the longevity and efficiency of the draft system.