How to Select the Right Beer Line Size for Long Draw Systems: Optimal Diameter & Length Guide
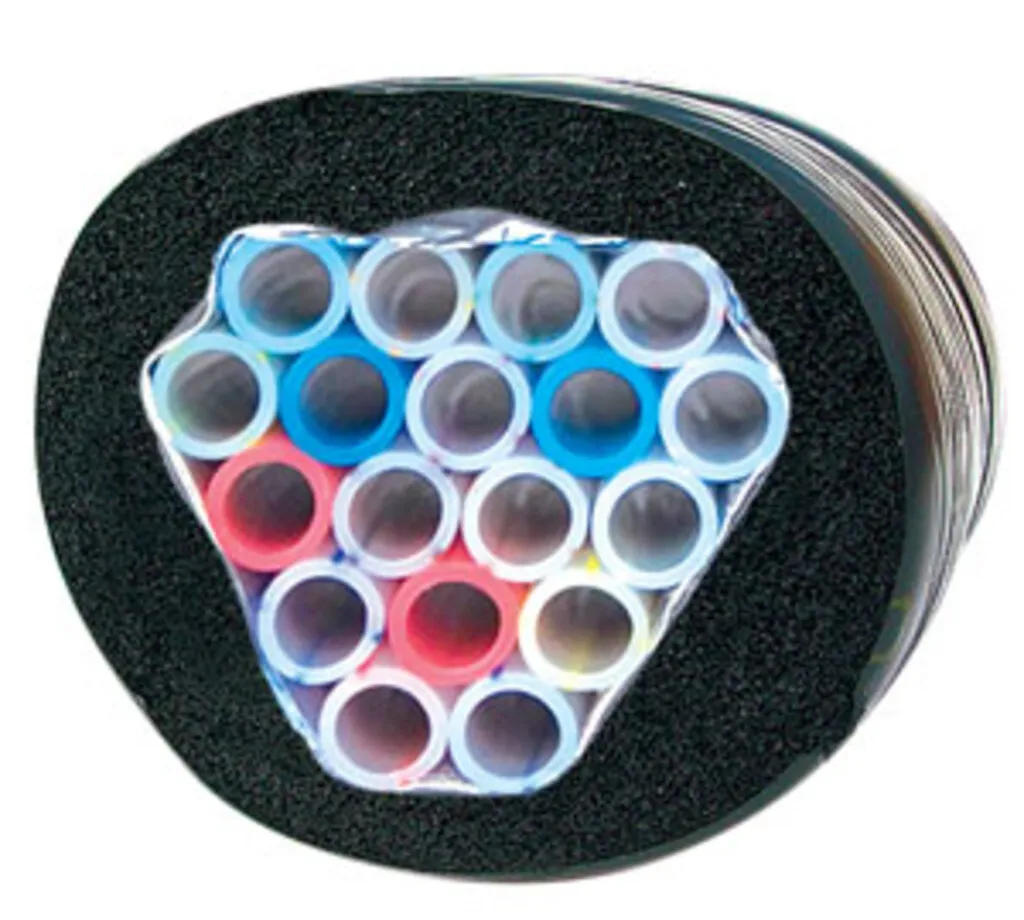
Selecting the right beer line size is a crucial factor in designing an efficient long-draw draft beer system. The size of the beer line directly influences the resistance level in the system, which needs to be balanced with the applied pressure to achieve the perfect pour. A line that is too small or too large can result in either excessive foaming or a sluggish flow, compromising the quality of the beer as well as the serving experience. Consequently, understanding and determining the optimal beer line size for a long draw system is not only about ensuring a clear, consistent flow but also about maintaining the integrity of the beer's taste and carbonation from keg to tap.
Long draw systems, typically used in bars and restaurants where the distance between the keg and the tap can be significant, require careful consideration of system design considerations for long draw. It involves intricate planning where the diameter and length of the line must be matched with the application of the correct CO2 pressure. Proper installation and regular maintenance are also key elements in ensuring that a draft beer system operates at its best. Industry standards and advanced insights on line resistance can offer guidance, but ultimately, every system may have unique requirements that need tailored solutions.
Understanding Beer Line Basics
Selecting the appropriate beer line size is pivotal for a proper long-draw beer system, as it ensures both quality and consistency of the dispensed beer. Proper understanding of components, pressure management, and material choices are foundational to the system's performance.
Components of a Draft Beer System
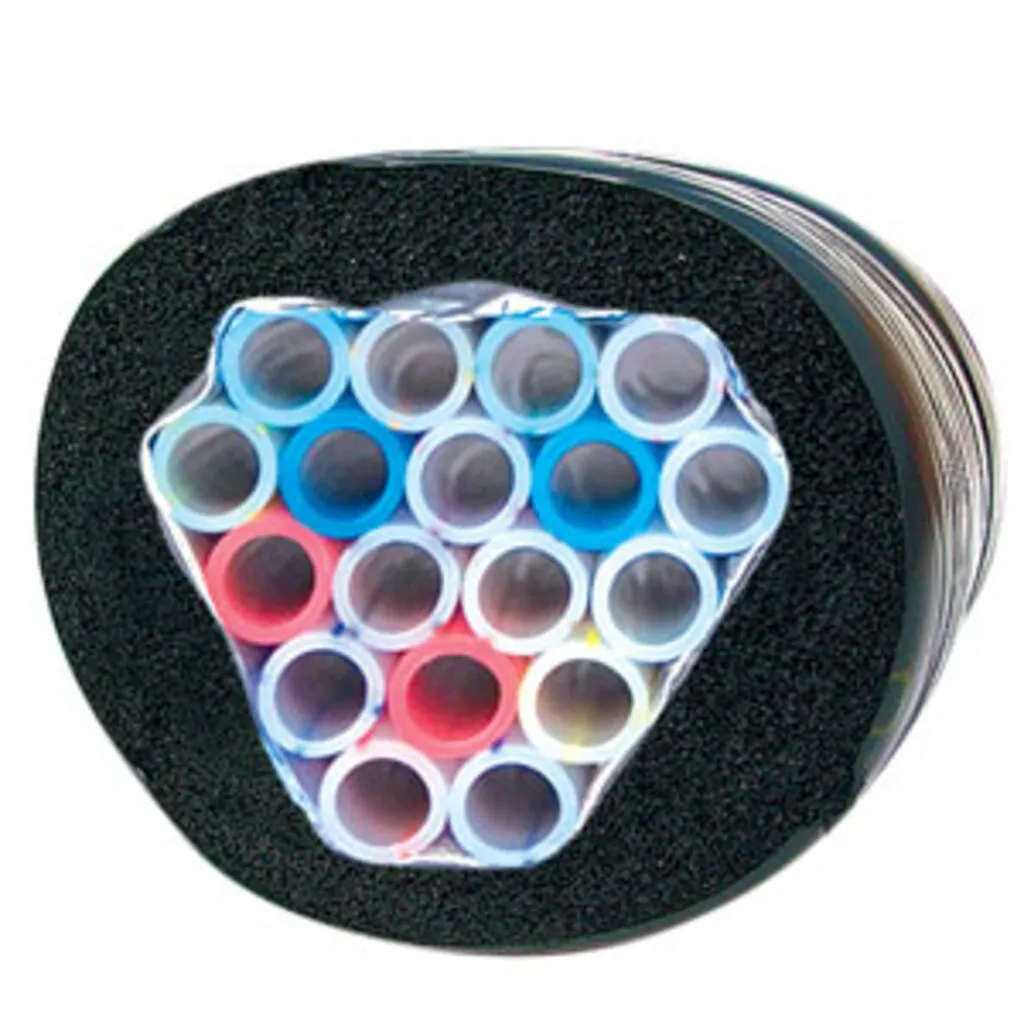
A draft beer system chiefly consists of a keg, which stores the beer, connected by tubing to a beer faucet from which the beer is served. CO2 or nitrogen tanks provide the necessary pressure for beer dispensing. Tubing, typically made of vinyl or stainless steel, plays a crucial role in quality en route to the tap.
The Role of Pressure in Beer Dispensing
Pressure is a critical consideration in a draft system. A balanced pressure, supplied by CO2 or nitrogen, pushes the beer from the keg through the lines without affecting its carbonation levels. Too little pressure and the beer will pour slowly or stop; too much, and the beer can become foamy or lose its desired taste profile.
Beer Line Material Considerations
For beer lines, material choice affects flavor and hygiene. Vinyl tubing is commonly used due to its low cost, but can impart flavors to the beer. Stainless steel is a premier option for its cleanliness and preservation of beer quality. Barrier tubing, offers superior resistance to flavor permeation and bacterial growth.
When incorporating these materials, one must consider the internal environment that they create for the beer as it moves from the keg to the faucet, and consequently, the impact on overall taste and quality.
Determining Optimal Beer Line Size
When setting up a long-draw beer system, selecting the right beer line size is critical for maintaining the quality of beer and achieving a perfect pour. The optimal size is determined by several factors including the diameter and length of the beer line and the temperature at which the beer is served.
Calculating the Right Diameter
The interior diameter (ID) of the beer line significantly affects the flow rate and the resistance beer faces when moving through the system. Typically, a larger ID, such as 3/8" (95 mm), is suitable for longer runs because it offers less resistance. Conversely, for shorter runs, a smaller diameter, such as 1/4" (64 mm), might suffice as it provides more resistance, which can be necessary to prevent the beer from flowing too quickly.
Selecting the Correct Length
The beer line length needs to be calculated to balance the system properly. This involves a precise formula that considers the set pressure of the CO2 regulator and the resistance factor associated with the chosen beer line's diameter. A common method for determining the right length is the line balancing equation, which helps ensure that the pressure is not too high or too low when the beer reaches the tap. A detailed example of such balance calculations is available at BrÜcrafter's Beer Line Calculator.
Influence of Temperature on Beer Line Size
Temperature impacts beer viscosity and CO2 solubility, which in turn affects the required beer line size. Serving beer at temperatures higher than recommended can result in excessive foaming, requiring a different line length or diameter to compensate. Conversely, cooler temperatures increase CO2 solubility, meaning less pressure is needed to dispense the beer, which could alter the beer line length consideration. Optimal temperatures and their influence on beer line lengths and sizing can be found through resources like BeerSmith's guide on Keg Line Length Balancing.
Balancing Your Draft Beer System
A well-balanced draft beer system ensures an ideal pour with the correct carbonation levels and flavor. Achieving this balance involves understanding the interplay between pressure and resistance in your beer lines.
The Science of Balancing
To achieve a balanced beer system, one must consider the resistance offered by the beer lines. This resistance needs to counterbalance the keg pressure to maintain the carbonation level as the beer is dispensed. Utilizing the right diameter and length of beer lines can help control the flow rate and maintain the correct carbonation level within the beer.
Working with Carbonation Levels
Carbonation levels in beer are measured in volumes of CO2, which indicates the amount of carbon dioxide dissolved in the beer. The industry standard for most ales and lagers is between 2.4 and 2.8 volumes of CO2. To maintain these carbonation levels from keg to tap, one should adjust the CO2 pressure accordingly.
Adjusting Pressure for Balanced Pouring
The pressure applied via the CO2 tank must be precisely calculated, considering the length and diameter of the beer line from the keg to the faucet. Calculation tools and formulas, like the Beer Line Calculator, can help. For example, with a set keg pressure, if the beer is flowing too quickly, it indicates low resistance in the lines, which requires either a longer line or one with a smaller diameter.
In summary, a balanced draft system is essential for a good beer experience, necessitating careful consideration of line size, carbonation levels, and applied pressure.
Installation and Maintenance Tips
Selecting the appropriate beer line size for a long draw draft beer dispensing system is crucial, but without proper installation and ongoing maintenance, even the best system can fail to perform. Ensuring the longevity and quality of the draft involves precise installation, regular cleaning, and prompt problem-solving.
Proper Installation for Performance
When installing a long draw system, it's vital to use insulation effectively to maintain the beer's temperature from the kegerator to the tap. A glycol chiller often accompanies long draw systems, where consistent temperatures are crucial for avoiding off-flavors. The trunk line—an insulated bundle of beer and coolant lines—should be properly sized and insulated, especially if running through areas subject to temperature fluctuations.
Routine Cleaning and Maintenance
For a draft system to pour perfect pints consistently, routine cleaning is non-negotiable. Beer lines should be cleaned at least every two weeks to prevent the build-up of bacteria, which can lead to off-flavors and health issues. Here are some recommended practices:
- Flush the lines with a caustic solution, followed by a clear water rinse.
- Inspect and clean faucets and keg couplers to remove any build-up.
- Check the glycol chiller for proper function and cleanliness.
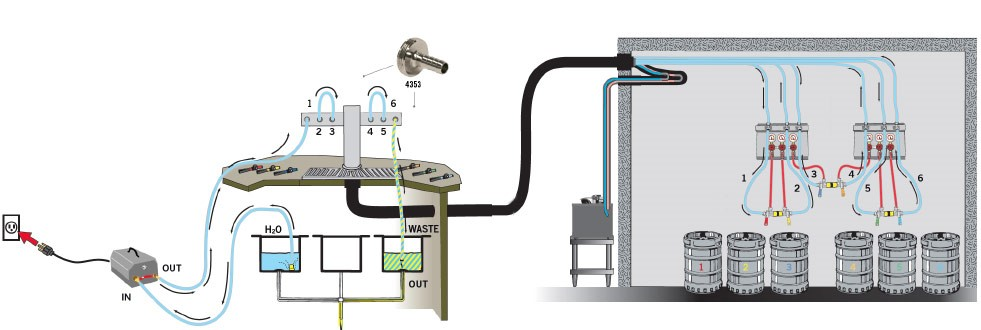
Dealing with Common Issues
Even with rigorous maintenance, issues may arise. If the beer is foaming excessively, it could be an indication of a temperature problem or an imbalance in the trunk line diameter or pressure. Signs of bacteria growth, such as sour or off-tasting beer, require immediate attention to cleaning protocols to ensure the integrity of the draft beer dispensing system. Regular audits of the system's components can preemptively address potential problems.
Advanced Insights on Line Resistance
In the complex arena of long draw beer systems, the significance of proper line resistance cannot be overstated. It is imperative for maintaining the beer's carbonation and overall presentation quality from keg to tap.
Understanding Restriction Value
The restriction value of a beer line correlates directly to its interior diameter and material. Narrower lines typically have higher restriction values, requiring more pressure to deliver beer efficiently. Ales and lagers commonly work well with standard line sizes, but attention to line resistance is crucial for optimal dispensing. For example, stouts and wheat beers may demand different resistance specifications due to their distinctive carbonation levels and pouring pressure needs.
Calculating Resistance for Various Beers
Resistance calculations are essential for serving different types of beers at their best. A lager might require a different line length compared to a stout due to its lower resistance level. A formula often used is R = (P - 1) / L, where R is resistance per foot, P is the dispensing pressure, and L is the line length in feet. For mixed gas systems, like those using nitrogen for stouts, an appropriate nitrogen regulator should be selected and calculations adjusted accordingly to account for the pressures specific to beer gas.
Incorporating Additives and Mixtures
When using mixed gas like a blend of CO2 and nitrogen, one must consider not only the resistance in the beer line but also the effect of the gas blend on the overall resistance. Nitrogen systems often require different pressure settings, balancing lower solubility in liquid with the need to push beer through a longer gas line. This influences the final resistance value, and accurate adjustments are crucial to prevent over- or under-carbonation, ensuring a smooth, high-quality pour.
Incorporating additives into beer that change its viscosity also alters the line resistance. One must factor in these changes to maintain the right flow rate and presentation at the tap.
System Design Considerations for Long Draw
Selecting the right components for a long-draw beer system is critical to maintaining the quality and consistency of the draft beer. Proper system design is essential to overcome challenges specific to long-draw beer dispensing.
Long Draw Specifics and Challenges
Long draw systems, also known as remote systems, are used when the keg and the tap are at a significant distance from each other. These systems typically involve running beer trunklines from the keg, where the beer is stored, to the taps, where it is served. The main challenges include maintaining the beer's temperature and preventing excessive foam.
- Distance: The greater the distance between the keg and the tap, the greater the potential for temperature changes.
- Temperature Fluctuations: A consistent temperature is crucial for maintaining beer quality, as fluctuations can result in foam issues or off-flavors.
- Pressure Requirements: Correct pressure settings are vital to push the beer through long lines without affecting its carbonation level.
A critical component is the keg coupler, which connects beer hose from the keg to the beer line. It must be compatible with the keg and create a tight seal to ensure no beer or gas is lost during dispensing.
Integrating Glycol Systems for Consistency
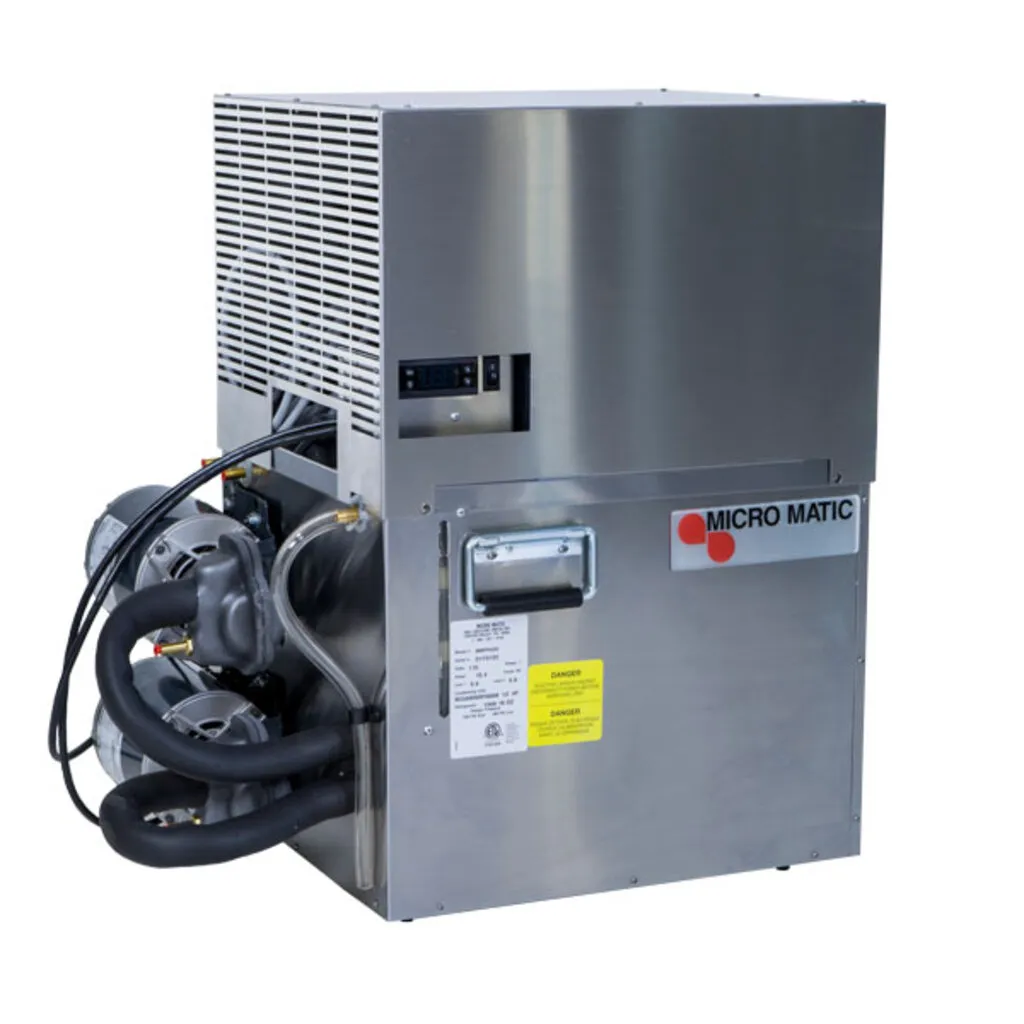
A glycol system is often integrated with long draw systems to keep the beer cool from keg to tap. This involves:
- Glycol Lines: These lines run alongside the beer lines in the trunkline, typically insulated to keep the beer at the correct temperature.
- Proper Insulation: Ensuring that the glycol and beer lines are adequately insulated is essential to prevent temperature gains.
- Balance: The diameter of the beer lines must be balanced with the power of the glycol system to ensure efficient cooling.
This cooling tower system plays a crucial role in a draft beer dispensing system that traverses long distances, such as in large bars or stadiums. It ensures that the beer served is consistently at the optimal temperature, enhancing the consumer's experience.
Summary
When selecting the appropriate beer line size for a long draw system, it's crucial to consider the total run length and the internal diameter of beer line.
Ideal Line Sizes:
- 1/4" (6.35 mm) I.D.: Best for short runs, higher resistance. 50' or Less
- 5/16" (7.94 mm) I.D.: Middle ground for resistance and flow. 100' or Less
- 3/8" (9.52 mm) I.D.: Suited for long distances, lower resistance
Selection Criteria:
- Distance: Longer runs typically require a larger diameter to reduce resistance.
- Resistance: Smaller diameters increase resistance; requires higher pressure to push the beer.
- Flow Rate: Aim for approximately 2 ounces per second; adjust line size accordingly.
- System Balance: Optimal diameter and length maintain beer quality and consistent flow.
Experts suggest that a 3/8" I.D beer line is effective at mitigating resistance over longer distances. For exact calculations on balancing a long-draw beer system, consider looking at some beer line size calculation examples.
In a long draw system, the trunk line, usually an insulated bundle housing beer and coolant lines, is another vital component. The trunk line aims to eliminate condensation and maintain the product's coldness from keg to glass, as described in a guide on long draw draft systems.
An understanding of these factors will help in making an informed decision to maintain a high standard of draft beer service.