Troubleshooting Beer Systems: Draft Beer Maintenance
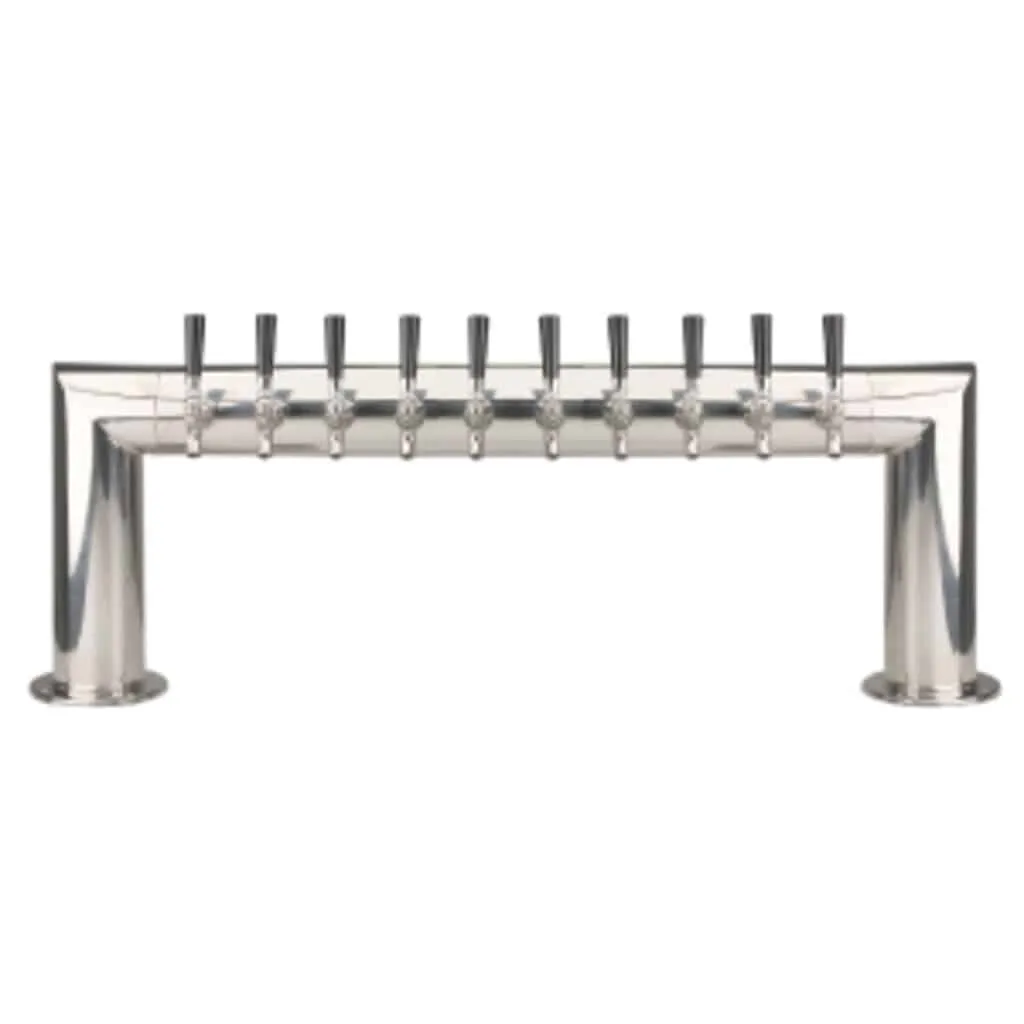
Beer lovers know that there's nothing quite like a perfectly poured draught beer. However, maintaining the quality of draught beer can be a challenging task, especially when issues arise in the beer dispensing system. This blog post aims to provide a comprehensive guide to troubleshooting beer systems, draft beer maintenance using insights from the Draught Beer Quality Manual.
The Importance of Proper Operation and Maintenance
Correctly dispensed draught beer is the result of proper temperature, proper gas pressure and mixture, and a well-maintained draught system. When a draft beer system is pouring well, it's easy to take all the variables for granted. However, improperly pouring beer can be frustrating and can result in loss of sales. Therefore, understanding how to troubleshoot common issues is crucial.
Common Problems and Solutions
Here are some common problems encountered in draught dispensing systems and their possible solutions:
1. Beer Foaming
This is a common issue that can be caused by various factors. The temperature at the faucet might be too warm or too cold. The beer line might be kinked or of the wrong size. The applied pressure might be too high or too low. The system might be dirty, or there might be a CO2 leak.To solve these issues, you can adjust the temperature control, change the beer line, adjust the CO2 regulator to the brewer's specification, or clean lines in the system, or check fittings, clamps, shut-offs, and regulators and replace as necessary.
2. No Beer at Faucet
This problem can occur if the CO2 bottle is empty, the regulator shut-off valve is closed, the CO2 bottle main valve is turned off, the keg is empty, or the coupler is not engaged.To fix these issues, you can replace the empty CO2 bottle with a full one, open the shut-off valve, turn on the CO2 bottle main valve, replace the empty keg with a full one, or tap the beer keg properly and engage the coupler.
Troubleshooting Different Systems
Different draught systems have unique features that require specific troubleshooting steps. Here are some guidelines for different systems:
1. Direct-Draw Systems
These systems require regular checks of temperature at the faucet, draft beer lines, and the keg box. The beer line length or diameter might need adjustment, and the CO2 regulator might need tuning. Regular cleaning of the system and replacement of defective parts are also crucial.
2. Air-Cooled Systems
For these systems, it's important to ensure that the blower fan's airflow is not obstructed and that the system is designed properly. The temperature of the beer in the keg should be checked regularly, and the minimum applied pressure should be adjusted according to correct temperature and to the brewer's specification.Remember, the single most common cause of problems encountered in draught dispensing systems and beer taps is temperature control. Therefore, the first step in solving any dispensing problem is to confirm that the liquid temperature of the beer in the glass or keg is where it's supposed to be.In conclusion, maintaining a draught beer system requires a good understanding of the system's operation and regular maintenance and cleaning equipment. By following the troubleshooting steps outlined in this guide, you can ensure that your draught beer remains of the highest quality, leading to satisfied customers and increased sales.
Glycol Cooled Systems
Glycol-chilled systems are commonly used for long-draw dispensing systems, servicing runs longer than 25 feet. These long draw draft systems use a separate chiller that pumps a chilled mixture of water and food-grade liquid propylene glycol through cooling lines parallel to and in contact with the beer lines. This helps maintain the beer's temperature as it travels from the keg to the faucet. However, like any system, glycol-chilled systems can encounter problems. Here are some common issues and their solutions:
1. Beer Foaming
Beer foaming can occur due to various reasons in a glycol-chilled draft system can. The temperature at the faucet might be too warm or too cold. The dispensing gas might be wrong, or the glycol pump might not be functioning properly. The gas regulators might be incorrectly set, or the applied pressure might be too low or too high.There could also be a kink in the beer lines somewhere between the cooler and beer tower. Once the beer lines are unobstructed move on to other things like temperature and applied pressure.To solve these issues, you can check the glycol chillers for proper operation and adjust the glycol bath temperature if it's too warm or too cold. Most systems are designed to operate between 28°F and 34°F, but you should check the unit manufacturer's specs. You can also adjust the CO2 regulator to the brewer's specification, replace defective parts, clean the system, or call a qualified service person to adjust the glycol chiller temperature or operation.
2. No Beer at Faucet
This problem can occur if the CO2 source, N2 source, or mixed gas bottle is empty, the regulator shut-off valve is closed, the gas bottle or bulk tank main valve is turned off, the keg is empty, or the coupler is not engaged.To fix these issues, you can replace the empty gas bottle with a full one, open the shut-off valve, turn on the gas bottle or tank main valve, replace the empty keg with a full one, or tap the keg properly and engage the keg coupler again.
Glycol Chiller Maintenance
Regular maintenance of the glycol chiller is crucial for the smooth operation of a glycol-chilled system. Here are some recommended maintenance practices:
- Check the temperature of the glycol bath every two weeks, making sure it is within the range specified by the manufacturer.
- Check motors monthly to confirm smooth-sounding operation and look for signs of overheating.
- Check pumps monthly for smooth-sounding operation; check connections and insulation for leaks or missing insulation.
- Inspect the condenser monthly for dirt and airflow obstructions and clean as necessary.
- Visually inspect trunk lines every six months for signs of ice buildup, insulation damage, and glycol leakage.
- Check the viscosity and condition of the glycol-water cooling mixture every six months. Test the freezing point every 18 months with a refractometer and adjust or replace the glycol mixture as needed.
Conclusion
By following these troubleshooting steps and maintenance practices, you can ensure the optimal operation of your glycol-chilled beer system, Air Cooled System, and Direct Draw System. Keeping your beer pouring and customers Happy.